Home Appliances Inspection - Appliance Quality Control Expertise
INSPECTION EXPERTISE
Home Appliances Inspection – Appliance Quality Control Expertise
Every year, numerous home appliances in Europe and America experience recalls, causing substantial financial and reputational losses. Amidst the pursuit of new technologies by Asian factories, especially in China, to meet rising demands for innovative and energy-efficient products, appliance quality can be enhanced. A vital approach to address this is through a robust home appliances inspection.
Â
Tetra Inspection is a global leader in household appliance quality assurance services. With a deep understanding of global standards and regulations like IEC, RoHS, and CE, our skilled inspectors ensure compliance. We identify risks, offer real-time reporting, and guide manufacturers through the certification process, guaranteeing top-tier home appliance products.
Â
To ensure your home appliance products are safe and compliant, book a home appliance inspection service today.
HOME APPLIANCES QUALITY CONTROL
The Importance Of Home Appliances Inspection
Home appliances have become integral to modern life, bringing households convenience, efficiency, and comfort. These appliances make daily tasks easier and more manageable, from washing machines and refrigerators to dishwashers and vacuums. However, ensuring these appliances’ safety, functionality, and quality is paramount. This is where home appliance inspection comes into play, especially regarding quality control during the manufacturing and distribution processes. Here are some common defects found during home appliance inspection.
Examples of Defects Found During Home Appliances Inspection:
Washing Machines:
- Water leakage due to faulty seals or hoses.
- Inaccurate water temperature control affects washing effectiveness.
- Imbalanced drum causing excessive vibration during operation.
Refrigerators:
- Faulty wiring causing fire hazard
- Inadequate cooling caused by malfunctioning compressors or refrigerant leaks.
- Faulty defrost system leading to ice buildup and poor cooling efficiency.
- Door seal defects causing temperature fluctuations and energy wastage.
Grills:
- Uneven heating due to malfunctioning burners or poor design.
- Corrosion and rust on grill grates impact food safety and taste.
- Gas leaks or ignition issues pose fire hazards.
Vacuums:
- Weak suction caused by faulty motors.
- Defective power cords or switches lead to intermittent operation.
- Easily worn-out brush rolls affect cleaning efficiency.
Ovens:
- Inaccurate temperature control affects cooking results.
- Uneven heat distribution leads to unevenly cooked food.
- Faulty door seals cause heat loss and energy inefficiency.
HOME APPLIANCES TESTING
Critical Elements Of Household Appliances Quality Control
Household appliances are more than just conveniences; they’re a crucial part of our daily lives. From ensuring our food stays fresh to washing our clothes, these appliances are indispensable. Therefore, maintaining their quality and ensuring their safety is paramount. But how is quality control for household appliances achieved in practice? Let’s dive into the key elements:
Raw Material Inspection:
Inspectors performs raw materials Inspections during the initial phase of manufacturing. For example, metals might be tested for tensile strength, corrosion resistance, or even composition. Plastic components might be subjected to durability and flame-retardant tests.
Performance Testing:
This involves running the appliance in various conditions to check its efficiency and durability. A washing machine, for instance, might be run continuously for hours to simulate years of usage or be tested at varying load levels and temperatures.
Functionality Tests:
Every feature the appliance boasts of is tested in real-world conditions. For a microwave, this could involve using all its cooking modes, checking if the timer functions correctly, or ensuring that the defrost setting works as intended.
Â
Consumer electronics demand a series of specialized tests, such as:
- Hi-Pot test
- Earth continuity test
- Power cord pull test
- Power consumption test
- Function test
- Current leakage test
- Full function test
- Rubbing test
- Frequency check
- Remote control range
- Memory size checkÂ
Design and Ergonomics:
The appliance design is reviewed for user-friendliness, ensuring it is intuitive and safe. Real-world trials can be set up, with testers using the appliances in simulated everyday scenarios to ensure the design meets ergonomic standards.
Safety Checks:
Each component is tested against possible hazards. This can mean checking for potential electrical short circuits, ensuring no sharp edges are exposed, or even testing the stability of the product (like a fridge) to ensure it doesn’t easily topple.
Energy Efficiency and Environmental Impact:
Appliances are tested for energy consumption to meet the set standards. This might involve running an air conditioner on its maximum setting, measuring power usage, or checking a dishwasher’s water consumption.
Â
Appliance QC Process
Home Appliance Inspection Process
The world of home appliances is vast and varied, with each product holding a significant place in our daily routines. Consumers and producers must ensure their quality, functionality, and safety. To accomplish this, a meticulous inspection process is adopted.
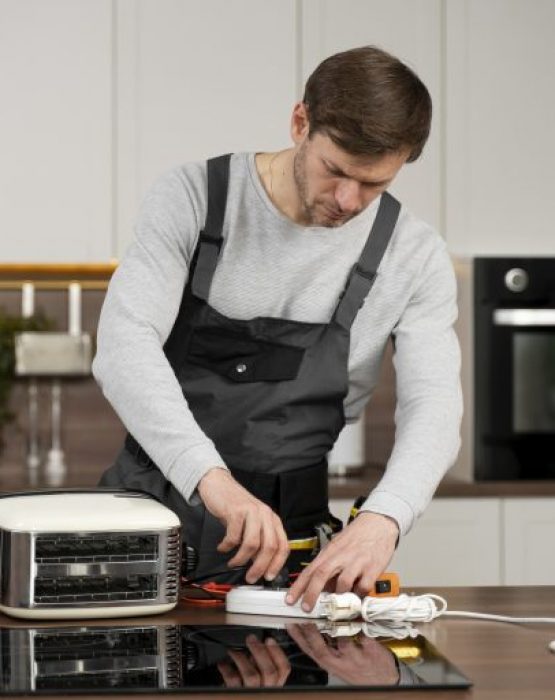
Initial Production Inspection, or IPI, is the first step of the quality control process, carried out when around 0-20% of the production is completed.Â
Here’s how it’s typically done:
Â
Factory Visit:Â Quality control professionals visit the manufacturing site.
Â
Raw Material Check:Â Inspectors verify the quality and adequacy of raw materials. They might test a sample against specific standards.
Â
Machinery Setup:Â Machines used in manufacturing are checked to ensure they are calibrated and functioning correctly.
Â
Initial Product Evaluation:Â The first products off the production line are checked for visible defects or discrepancies.
Â
Feedback and Corrections:Â In case of any issues, feedback is provided immediately, allowing manufacturers to rectify errors before bulk production begins.
During Production Inspection (DUPRO)Â is carried out when approximately 20-80% of the production is completed. It helps in monitoring the quality during the manufacturing process.
Â
Sampling Verification:Â A certain number of products, based on internationally recognized statistical standards, are chosen for inspection.
Visual Inspection:Â Products are checked for any visible defects or inconsistencies.
Â
Functional Tests:Â Randomly selected products are tested to see if they function as intended.
Â
Assembly Check:Â Inspectors ensure the products are assembled correctly and that steps are completed on time.
Â
In-line Corrections:Â Any deviations from the standard process or quality are corrected immediately.
ThePre-shipment Inspection is carried out when the production is 80-100% complete and at least 80% of goods are packed; this is the final inspection before the products are shipped.
Â
Random Sampling:Â Based on accepted quality limits (AQL), a sample of products is chosen for inspection.
Â
Detailed Visual Inspection:Â Inspectors conduct a thorough visual inspection to ensure no defects.
Â
Functional and Safety Tests:Â Appliances are tested for functionality. Safety tests like the Hi-Pot or Earth continuity test might also be performed.
Â
Packaging and Labeling:Â Inspectors ensure products are adequately packed, and labels like barcodes, shipping marks, and other essential details are accurate.
Main Tests Performed During Consumer Electronics Inspection
Applicable Standards For Appliance Quality Control
Ensuring household appliances are safe, durable, and function as intended is not just about thorough inspections. It also involves adhering to various standards that set the criteria for a quality appliance. Here are the standards applicable to Appliance Quality Control
- International Electrotechnical Commission (IEC) Standards: The IEC establishes worldwide standards for all things electrical. These are internationally recognized, and many countries use them as a basis for their national standards. When an appliance, say a blender, is manufactured, its design and functions are checked against the IEC’s criteria. This includes checking the blender’s safety features, its electrical consumption, and even how much noise it makes. Manufacturers might have a checklist derived from IEC standards to ensure compliance.
- RoHS Compliance: The Restriction of Hazardous Substances Directive (RoHS) limits using specific hazardous materials in electronic products. Factories often require suppliers to provide RoHS certificates for components. Additionally, random testing of components can be done in labs to ensure they don’t contain restricted substances.
- CE Marking: This certification mark indicates conformity with health, safety, and environmental protection standards for products sold within the European Economic Area (EEA) Before a product like a microwave can have a CE mark, it must undergo a series of tests. If it passes, it’s then given a Declaration of Conformity (DoC), which is kept on record. This declaration allows the manufacturer to place the CE marking on their product legally.
- Energy Star Certification:This is more of an efficiency standard, but it’s become synonymous with quality for many consumers. Appliances with this certification are more energy-efficient than their counterparts. Let’s consider an air conditioner. If it’s being considered for Energy Star certification, it would be tested for how much electricity it consumes under various conditions. Only after it meets the stringent efficiency criteria will it be certified.
- ISO Standards: The International Organization for Standardization (ISO) develops and publishes many international standards, some relevant to appliances, like ISO 9001, for quality management. Manufacturing units aim to get ISO certified by adhering to the standards set. For instance, a factory producing refrigerators might adopt a comprehensive quality management system, ensuring that every refrigerator is consistent in quality and performance.
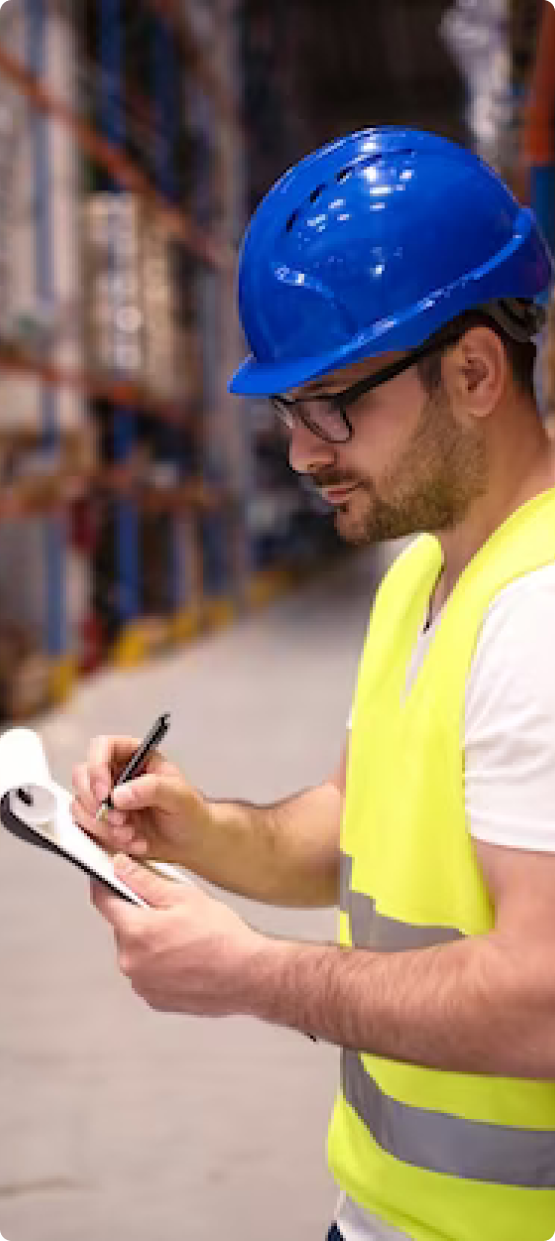
How Tetra Inspection Can Help With Home Appliance Inspection
Trained And Experienced Inspectors
Tetra Inspection’s team comprises highly trained professionals in household appliance inspection. Their rich experience enables them to understand the intricacies of different products, ensuring precise and accurate assessments.
Real-Time Reporting
At Tetra Inspection, our clients are kept in the loop with real-time reporting. We provide detailed inspection reports, complete with images and inspection results, which are shared promptly, facilitating quick decisions.
Compliance With International Standards
Tetra Inspection ensures that the products align with international standards like IEC, RoHS, and CE Marking. We guide manufacturers through compliance, providing the necessary support to ensure products meet the required legal obligations.
Assistance With Certification Processes
From acquiring ISO Certification to fulfilling CE Marking standards, Tetra Inspection can guide manufacturers, importers, and brands through the complicated certification landscape, ensuring smooth sailing.
Schedule Your Home Appliances Inspection Today
Count on our team of experienced professionals for thorough home appliance inspections, effectively mitigating risks and ensuring full compliance with global standards.
Â
BLOG
Related Articles
shipment, minimizing risks and ensuring compliance with international standards.