Pre-Shipment Inspection - Ensuring Quality and Compliance
Pre-Shipment Inspection: Ensuring Quality And Compliance
What Is Pre-Shipment Inspection And Why Is It Important?
Reducing Risks for Buyers and Sellers
Ensuring Product Quality and Compliance
Facilitating Timely Deliveries
Supporting Ethical and Sustainable Practices
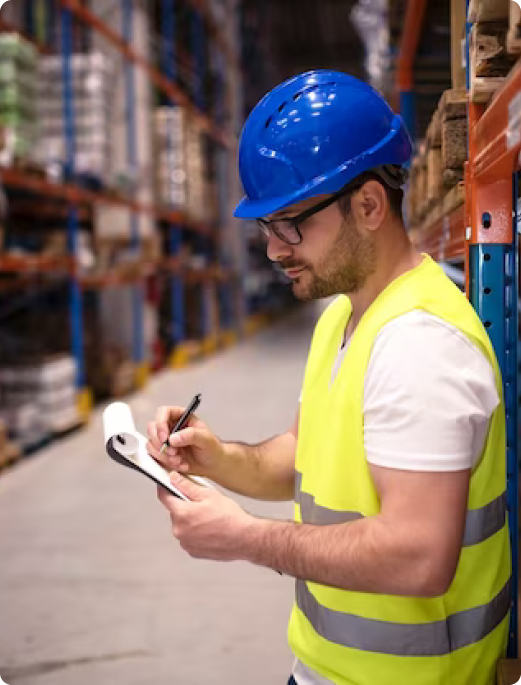
Benefits Of Pre-Shipment Inspection
One of the primary advantages of PSI is that it helps businesses ensure that the goods meet the buyer’s requirements and specifications. This reduces the risk of costly product rejections and returns, improving customer satisfaction and significant cost savings. Moreover, PSI helps identify any issues or defects in the products before shipment, enabling prompt corrective action and preventing potential problems that could impact the timely delivery of goods. This is crucial in ensuring that the supply chain remains efficient and optimized.
In addition to the benefits mentioned above, PSI also provides an extra layer of protection against fraud and counterfeit goods, particularly in industries where product safety and quality are crucial. This is because pre-shipment inspections verify the authenticity and quality of the goods, which helps businesses protect their brand reputation and prevent any legal or regulatory issues. By ensuring that their products comply with industry standards and regulations, businesses can also demonstrate their commitment to providing safe and reliable products to their customers.
Pre-Shipment Inspection Process: What To Expect
Tetra Inspection‘s expert inspectors will visit the production site or factory to conduct a thorough inspection of your products. This is done when the production is completed 100%, and at least 80% of your order has been packed and ready for shipping.
The inspectors will verify the quantity of products and packaging, ensuring that everything is accurate and safe for transportation.
Using the Acceptance Quality Limit (AQL) method, the inspectors will randomly select a sample of products for inspection, ensuring that the results are statistically accurate.
Tetra Inspection will verify that the products conform to the specifications agreed upon in the contract, including size, color, weight, and packaging.
The selected sample will undergo rigorous testing to ensure that it functions properly and meets safety standards. This includes various tests such as pull tests, fatigue tests, and stretch tests for garments, and safety tests for electronics and mechanical products.
Tetra Inspection will check for visible defects and classify them as major, minor, or critical defects. The inspectors will make a pass or fail decision based on predetermined tolerance levels.
A GUIDE FOR BRANDS AND IMPORTERS
When To Schedule A Pre-Shipment Inspection
- Production timeline: Schedule the inspection after at least 80% of the order has been produced. This allows for a more representative sample of the goods and helps identify potential issues before shipment.
- Production timeline: Account for the time required to address any identified issues and re-inspect the goods, if necessary. PSI should ideally be conducted 1-2 weeks before the shipping deadline to ensure enough time for corrective actions.
- Seasonal factors: Consider potential seasonal constraints, such as holidays or peak manufacturing periods, which may impact production, inspection, and shipping schedules.
- Customs and regulatory requirements: Be aware of any regulatory compliance deadlines or specific requirements that may impact the PSI process.
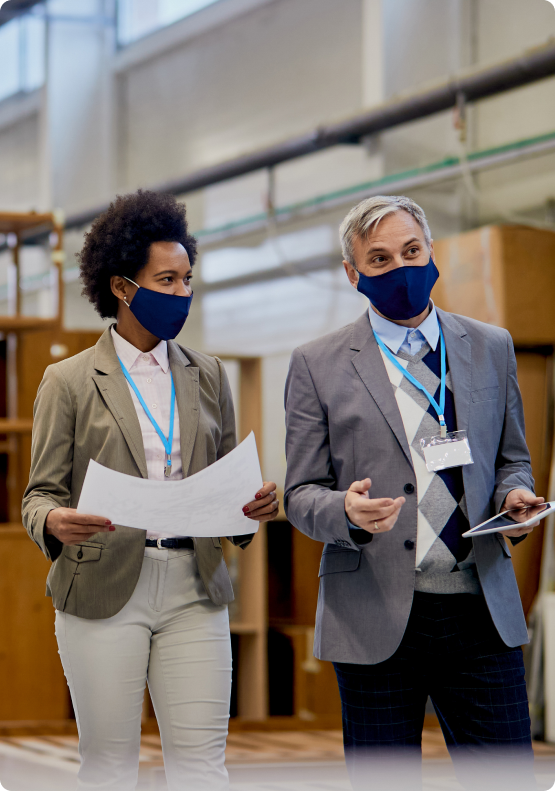
Initial Product Checking
During Production Inspection
20-40% Production Complete
Performed when around 20-80% of the production is complete to identify issues early on and monitor production progress.
Pre-Shipment Inspection
80-100% Production Complete
Scheduled when 80-100% of the production is completed and at least 80% of the products are packed.
Container Loading Check
100% Production Complete
Comprehensive Checklist
What Checks Are Carried Out During A Pre-Shipment Inspection?
Pre-shipment inspections (PSIs) are conducted to safeguard product quality, safety, and compliance before shipping to their destination. At Tetra Inspection, we pride ourselves on our meticulous approach to PSI, offering clients the confidence that their goods meet the highest industry standards. Here is the comprehensive checklist of the checks carried out during a Pre-shipment Inspection to provide you with a clear understanding of what to expect.
Visual Inspection
- Packaging Inspection: We examine the packaging materials to ensure they meet your specifications and provide adequate protection during transit..
- Checking labeling: We verify that the labels on the products and packaging are accurate and comply with relevant regulations.
- Inspecting product appearance: We scrutinize the products for any visual defects, such as scratches, dents, or color discrepancies.
Functional Testing
- Performance assessment: We test the products’ functionality to ensure they operate as intended and meet your performance requirements.
- Safety checks: We verify that the products comply with applicable safety standards, such as electrical safety, mechanical safety, and chemical safety.
- Reliability testing: If applicable, we perform stress tests to assess the products’ durability and reliability under normal and extreme conditions.
Quantity Verification
- Confirming order quantity: We count the total number of products to ensure they match your order.
- Sampling plan: We follow internationally recognized sampling plans, such as ANSI/ASQ Z1.4 or ISO 2859-1, to determine the appropriate sample size for inspection.
- Random selection: We select samples randomly to ensure an unbiased inspection result.
Dimensional Inspection
- Measuring dimensions: We measure the products’ dimensions to ensure they are consistent with your specifications.
- Tolerances: As specified in your requirements, we confirm that the products’ dimensions fall within the acceptable tolerance range.
- Assessing workmanship: We evaluate the quality of workmanship, such as seams, stitching, and assembly, to ensure they meet your quality standards.
Documentation Review
- Reviewing production records: We scrutinize production records, including raw material certificates, production logs, and test results, to ensure traceability and compliance.
- Verifying shipping documents: We review the shipping documents, such as the commercial invoice, packing list, and bill of lading, to confirm their accuracy and completeness.
- Ensuring regulatory compliance: We ensure that the products comply with the relevant regulations and certifications, such as CE, RoHS, and REACH.
Trust Tetra Inspection
Why You Should Trust Tetra Inspection For Your Supplier Verification Audit Needs
At Tetra Inspection, our comprehensive pre-shipment inspection checklist covers every crucial product quality and compliance aspect. When you collaborate with us, you can have confidence that your products will adhere to the most stringent industry standards, minimizing potential safety hazards and safeguarding the integrity of your brand.
Expertise Of Experienced Inspectors
Tetra Inspection employs skilled inspectors knowledgeable in global export regulations, ensuring inspections are carried out by professionals well-acquainted with your target country’s specific requirements.
Detailed Reports With Digital Evidence
Open Communication And Collaboration
We value open communication and collaboration, that allows us to tailor our services to our clients’ specific needs and preferences.
Global Coverage
Schedule Your Pre-Shipment Inspection Today
shipment, minimizing risks and ensuring compliance with international standards.
Common Questions About
Pre-Shipment Inspection, Answered (FAQ)​
The cost of a pre-shipment inspection depends on the pricing plan you choose. Here are the available options:
Â
Standard Rate:
- Price: $240 per man-day
Monthly Plan
- Price: $189 per man-day (over 20% savings)
- Billed Monthly at $1,899 for 10 inspections across Asia
Annual Plan (Recommended):
- Price: $158 per man-day (over 35% savings)
- Billed Monthly at $1,584 for 120 inspections across Asia (12 months subscription)
- Â
Our pre-shipment inspection services boast the fastest turnaround time in the industry, thanks to our extensive network of 350+ inspectors across 40 countries. We can inspect with as little as 12-24 hours’ notice and deliver the inspection report on the same day the inspection is completed.
If quality issues are discovered during the inspection, our inspector will thoroughly document the defect with images and categorize it as major, minor, or critical. They will report their findings to you. Based on the inspections report, you can decide whether to:
Â
- Accept the products as they are, considering the defects are within an acceptable range.
- Request the supplier to fix the issues before shipment and schedule a re-inspection to ensure the corrections have been made.
- Reject the products and negotiate with the supplier for replacements or refunds.
While pre-shipment inspections can be conducted on various products, there may be cases where inspections are not possible or prohibited due to legal or regulatory restrictions. Examples of such products include:
Â
- Hazardous materials or substances that pose a risk to the inspector’s safety or health.
- Products under strict intellectual property or trade secret protection restrict access to authorized personnel only.
- Prohibited or illegal items: Items banned or restricted by international law, local regulations, or the inspection company’s internal policies.
BLOG
Related Articles
shipment, minimizing risks and ensuring compliance with international standards.