Â
If you are outsourcing from abroad, chances are you have to rely on a network of suppliers, each with their own processes and quality control measures. While some suppliers consistently deliver top-notch products, others may require a closer look.Â
Â
This is where a random inspection comes in – a strategic tool for assessing quality and mitigating risk within your supply chain. They offer important data to ensure your products meet specifications and arrive defect-free.Â
Â
In this comprehensive guide, we will discuss everything about Random Inspection, equipping you with the knowledge to determine when they are necessary, select the most appropriate method, and navigate the inspection process itself.
Â
Let’s begin.
Â
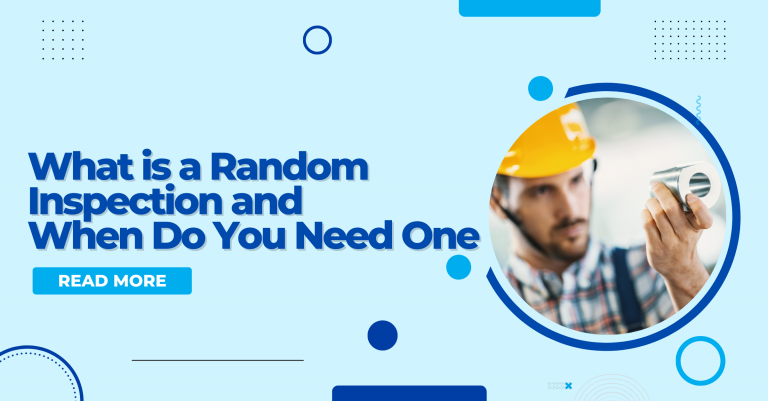
What is a Random Inspection?
A random inspection is a surprise check-up on a batch of products before they’re shipped to you. Instead of examining every single item, inspectors choose a random sample. It’s like picking names out of a hat – each product has an equal chance of being inspected.
Â
This approach ensures the factory can’t predict which items will be checked, giving you a more accurate picture of the overall quality. Inspectors thoroughly examine these samples, looking at things like conformity to specifications (size, color, functionality), presence of defects (scratches, dents, malfunctions), proper labeling and packaging, and adherence to safety regulations.
Â
Unlike a full inspection of every product, random inspections focus on a representative sample. This allows you to get a good idea of the overall quality of your shipment without having to hold up production or incur significant costs. The specific aspects inspected will vary depending on your product type. It could include checking for the correct number of items, verifying parts and materials, examining packaging for damage, and ensuring the products themselves are free from defects.
Â
Choosing Between Random Inspection and Full Inspection
There are two main ways to check the quality of a large batch of items: inspecting every single one (full inspection) or inspecting a carefully chosen sample (random inspection).
Â
Full inspection means looking at each and every item in the batch. This guarantees that any defects will be found. However, it can be very time-consuming and expensive, especially for large batches.
Â
Random inspection involves checking a smaller selection of items chosen at random from the entire batch. This is much faster and cheaper than full inspection. However, there’s always a slight chance that the chosen sample might not perfectly reflect the quality of the entire batch.
Â
Here’s a quick guide to help you decide which method is best for you:
Â
Choose Full inspection if:
- The consequences of a defect are very serious (e.g., medical equipment)
- The batch is small
Choose random inspection if
- The cost and time of full inspection are too high
- You are confident in the supplier’s quality control processes
- A small percentage of defects is acceptable
In many cases, a combination of both methods can be used. For example, you might do a full inspection on the first few batches from a new supplier, and then switch to random inspections if the quality is consistently good.
Â
When are Random Inspections Necessary?
Random inspections are a cost-effective way to check product quality, but are they always necessary? Here’s a quick breakdown:
Â
- Cost vs. Risk: While full inspections guarantee every item is checked, they are a bit expensive. On the other hand, Random Inspections save money, but there’s a chance the random sample might miss hidden defects. So, weigh the cost of potential problems against the cost of inspections.
- Supplier Reliability: Â New suppliers or those with a history of inconsistency are prime targets for random checks. Established partners with a proven track record might not need them as often.
- Product Complexity: Â Complex or safety-critical products require stricter quality control. Random inspections may not be as effective as full inspection. Depending on your product category, determine which one is more appropriate for you.
The Random Inspection Process Explained
1. Planning and Preparation:Â
Defining Your Goals:Â
The first step is to clearly define what you want to achieve with the inspection. Are you looking for minor cosmetic defects, major functionality issues, or simply ensuring conformity to pre-defined specifications? Knowing your objectives helps tailor the inspection to identify the most critical areas.
Choosing the Inspection Point:Â
The timing of the inspection plays a crucial role. Options include:
- During Production: This allows for early detection and correction of issues before they become widespread.
- Pre-Shipment: Offers a final safety net to ensure quality before products leave the factory.
- Container Loading Check: Verifies the correct quantity and condition of goods being loaded for shipment.
Developing the Sampling Plan:Â
- Statistical methods and predetermined acceptable quality levels (AQL) come into play here. This dictates the number of items to be randomly selected from the entire batch. The AQL essentially defines the maximum number of defects considered acceptable within a given sample size.
- Crafting the Inspection Checklist: This detailed document outlines the specific aspects to be examined during the inspection. Depending on your product, the checklist might cover:
- Dimensional Accuracy: Are the products within the specified size tolerances?
- Functionality: Do they operate as intended?
- Material and Component Verification: Are the correct materials and components used?
- Packaging Integrity: Is the packaging free from damage and adequate for protecting the product during transport?
- Labeling Compliance: Do the labels meet all legal and regulatory requirements?
2. Sample Selection and Inspection:Â
Â
- Random Selection:Â An independent third-party inspector or a designated personnel from your team will use a pre-defined randomization method to choose the samples from the production line or finished goods inventory. This ensures an unbiased selection, preventing the supplier from manipulating the inspection process.
- Physical Examination:Â
- Each chosen item undergoes a meticulous examination against the established checklist. The inspector meticulously documents their observations, including:
- Defect Identification: Noting any deviations from specifications or defects encountered, such as scratches, dents, malfunctioning components, or missing parts.
- Defect Severity: Categorizing the defects based on their severity – minor cosmetic blemishes, major functionality issues, or safety hazards.
- On-Site Testing (Optional): Depending on the product type, specific tests might be added to the mix. For example, drop tests are performed to check the integrity of electronics to assess durability or stress tests for furniture to gauge strength.
3. Analysis and Reporting:
- Data Analysis: The inspector meticulously analyzes the collected data. They compare the number of defects found against the predetermined AQL limits. This provides a clear picture of the overall quality of the batch and ensures that it meets the acceptable level of defects outlined in the AQL
- Comprehensive Inspection Report: A detailed report is generated, outlining the entire inspection process. This includes:
- Description of the inspected products and batch size.
- Details of the sampling plan and AQL levels used.
- A breakdown of the identified defects, including their type, severity, and photographic evidence.
- The final verdict – “pass” or “fail” for the inspected batch.
4. Follow-Up Actions:Â
- “Pass” Verdict: If the inspected batch meets the AQL and no critical defects are identified, production or shipment can proceed as planned.
- “Fail” Verdict: This triggers a series of potential actions depending on the severity of the defects. Options might include:
- Rework: The supplier might be required to rework the defective items to meet specifications.
- Negotiation: Negotiations with the supplier on price adjustments or concessions may occur.
- Batch Rejection: In extreme cases with widespread or critical defects, the entire batch might be rejected.
What Gets Checked During a Random Inspection?
There are three main areas of focus during a random inspection:
Â
Conformity to Specifications:
Every aspect of the product is scrutinized, including quantity, components, assembly, aesthetics, functionality, dimensions, labeling, and packaging. A pre-defined checklist ensures a thorough evaluation.
Â
Number of Cosmetic Defects: The inspector randomly selects samples and meticulously counts defects, comparing them against the agreed-upon AQL limits.
Â
On-Site Testing: Depending on the product type, specific tests might be conducted. For example, a drop test might be performed on a sample of electronic gadgets.
Â
Limitations of Random Inspections
While random inspections offer a valuable tool for ensuring compliance or quality, they do have some inherent limitations. Here’s a breakdown of the key challenges:
Â
- Incomplete Picture: Random inspections only examine a selected sample, not everything. There’s always a chance that issues might exist outside the inspected items.
- Timing Issues: By their random nature, inspections might occur when problems aren’t happening. For instance, an unexpected inspection at a factory might not catch a recurring issue that only happens during a specific shift change.
- Hidden Problems: Some issues might be cleverly concealed or difficult to detect during a brief inspection. This could be due to limitations in access or the need for specialized equipment.
How Tetra Inspection Can Help
Whether you require a Random Inspection or comprehensive Full Inspections, Tetra Inspection offers a one-stop solution. With a network of over 500 experienced inspectors across 40 countries, we can ensure your products are evaluated within 24 hours.Â
Â
Our meticulous inspectors deliver detailed inspection reports on the very same day, allowing you to make informed decisions quickly. Â
Â
Contact Tetra Inspection today to learn more about our product inspection services.
Â