Quality control is essential for businesses to ensure their products meet the highest standards, resulting in satisfied customers and a successful brand. Developing a robust quality control plan is critical for optimizing processes, preventing product quality concerns, and achieving long-term savings in both time and money.
Â
Here is a step-by-step guide that will assist you in developing a customized quality control plan that is both efficient and effective for your business. We will cover the essential elements and provide helpful examples to illustrate each point better.
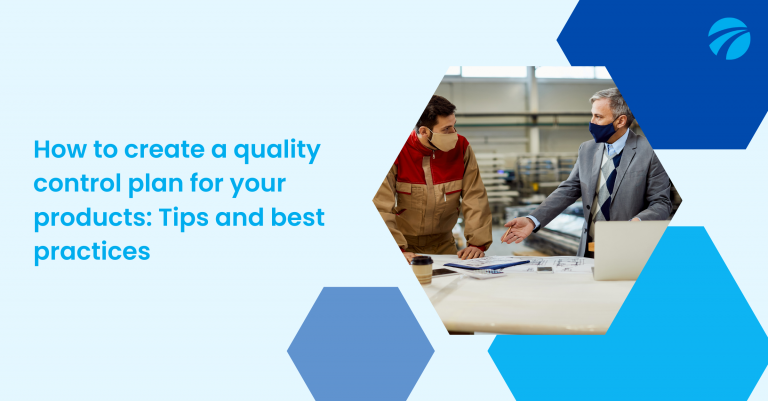
1. Establish Clear Objectives
The first step in developing a quality control plan is establishing clear product quality objectives. Consider the expectations of your target customers and define what quality means for your brand. Make sure to include detailed product specifications, such as size, shape, materials, components, colors, and any other relevant information. This will help you hold your manufacturer accountable and prevent quality fade due to factory modifications.
Â
If you manufacture artisanal candles, your objectives could include the following:
Â
- Using eco-friendly materials.
- Ensuring a consistent burn time.
- Maintaining a specific scent strength throughout the candle’s lifespan.
2. Define Steps, Practices, and Procedures
Efficiency is critical in managing quality control. Here are the steps you should follow to ensure consistent quality throughout the production process: This could include quality checks at various stages of production, communication with manufacturers and suppliers, and addressing any issues. A comprehensive plan that is thoroughly documented ensures the avoidance of any overlooked steps and promotes consistency in your processes.
Â
Â
In the case of artisanal candles, steps could include:
Â
Â
- Regular checks on the quality of wax and scents used.
- Monitoring the production process for consistency in size and shape.
- Conducting burn tests to ensure burn time and scent strength meet your objectives.
3. Allocate Responsibilities
Outline the distinct roles and responsibilities assigned to our team members for effectively managing and implementing the quality control plan. This could include designating a quality control manager, assigning inspection and testing responsibilities, and determining who will communicate with manufacturers and suppliers.Â
Â
Transparent allocation of responsibilities will help prevent miscommunication and ensure that issues are promptly addressed.
4. Set Quality Control Standards
Quality Control Standards are essential for holding manufacturers accountable for meeting your product specifications. One widely used statistical tool for managing quality is the Acceptance Quality Limit (AQL). AQL helps you determine the maximum number of defective products allowed in a sample before the entire batch is unacceptable. Set appropriate AQL levels for your products to meet your quality objectives.
5. Implement Inspection, Product Testing, and Audits
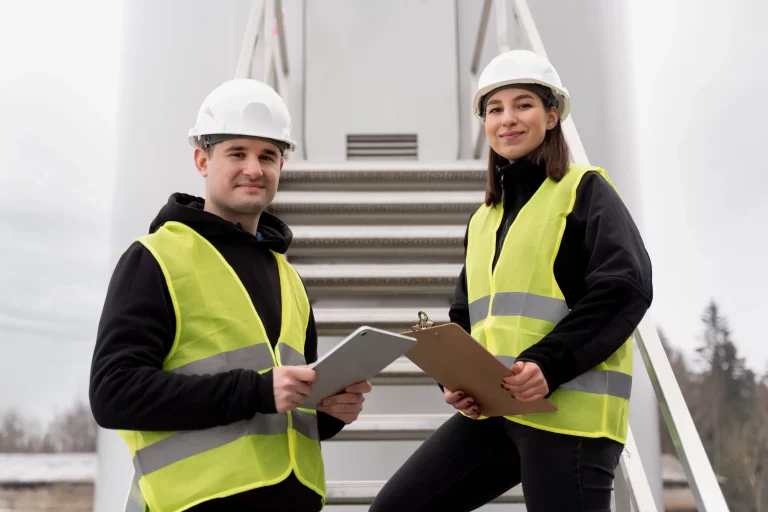
Three essential tools for managing supplier quality are product quality inspections, factory audits, and laboratory testing. Regular inspections, audits, and tests will help you identify issues early and ensure that your products consistently meet quality standards. Document your inspection, product testing, and audit schedules in your quality control plan.
6. Plan for Modifications
Your quality control plan should be flexible enough to accommodate product specifications or manufacturing process changes. Establish procedures for updating your plan to remain relevant and practical. This could include revising product specifications, adjusting AQL levels, or changing inspection and testing schedules.
7. Measure Success and Failure
Evaluate the success of your quality control plan by regularly reviewing inspection, audit, and lab test reports. Track trends over time to identify areas for improvement and ensure that your shipments and suppliers consistently meet your quality standards. Include your methods for measuring success and failure in your quality control plan.
How Tetra Inspection Can Help with Quality Control Inspection
Tetra Inspection is a professional third-party inspection company specializing in quality control for businesses of all sizes. Our highly experienced inspectors conduct pre-production, in-process, and pre-shipment inspections, ensuring products meet your specifications. We develop customized inspection protocols tailored to your unique requirements and provide comprehensive reports with photographs, test results, and observations for informed decision-making.
Â
Â
In addition to product inspections, we perform factory audits to evaluate supplier compliance with international standards and identify potential risks. Partnering with Tetra Inspection streamlines your processes, detects issues early, and guarantees consistent product quality.Â
Â
Contact us today for tailored inspection services and factory audits, and let our experts support your quality control plan.Â
Â