What is IQC Inspection?
IQC inspection, also known as incoming quality control inspection, is a vital process that ensures that the raw materials and components used in the manufacturing of a product meet the required standards and specifications. The purpose of IQC inspection is to detect and correct defects early in the production process, reducing the risk of producing defective products and the associated costs of scrap and rework.
Â
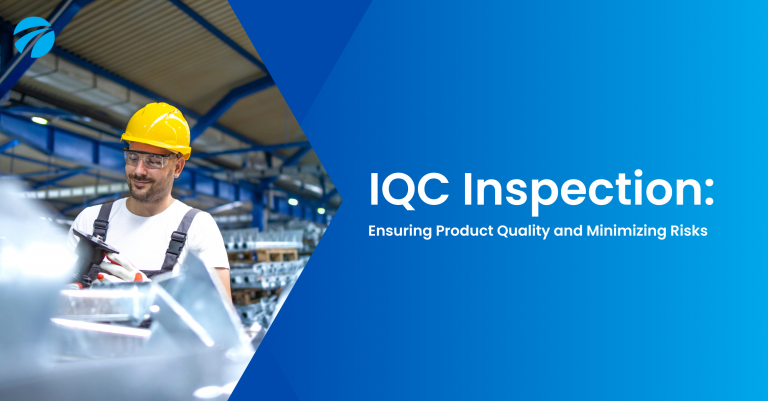
Types of IQC Inspections
IQC inspection can be divided into three main categories:
Â
- Initial Production Check (IPC)
- During Production Inspection (DUPRO)
- Raw Material Inspection.
Initial Production Check (IPC)
An initial Production Check (IPC) is a quality control inspection that is performed on the first batch of goods produced by a factory. The purpose of an IPC is to ensure that the factory is following the correct procedures and specifications and that the goods produced meet the required quality standards.
Â
Example: Initial Production Check (IPC) of a garment factory, to check the quality of the fabric and the stitching of the clothes
During Production Inspection (DUPRO)
During Production Inspection (DUPRO) is a quality control inspection that is performed while the factory is still producing goods. The purpose of a DUPRO is to ensure that the factory is maintaining the required quality standards throughout the production process and that any issues are identified and addressed in a timely manner.
Â
Example: During Production Inspection (DUPRO) of a toy factory, to check if the toys are meeting safety standards.
Â
Raw Material Inspection
Raw Material Inspection is a quality control inspection that is performed on the raw materials used in the production process. The purpose of raw material inspection is to ensure that the materials used meet the required quality standards and that they are suitable for the intended use.
Â
Examples: Raw Material Inspection of a food manufacturing factory, to check the quality of ingredients used in the production.
IQC Inspection Process
The IQC inspection process typically includes several key steps, including sample selection, inspection criteria, inspection methods, and inspection documentation and reporting.
Sample Selection
The first step in the IQC inspection process is to select a representative sample of the raw materials or components to be inspected. The size of the sample will depend on the type and complexity of the product, as well as the size of the batch or shipment.
Inspection Criteria
The next step is to establish the inspection criteria, which will be used to evaluate the sample. The inspection criteria should be based on the product specifications and industry standards.
Inspection Methods
The inspection methods used will depend on the type of product and the inspection criteria. Common methods include visual inspection, measurement, and product testing.
Inspection Documentation and Reporting
The final step in the IQC inspection process is to document and report the results of the inspection. The documentation should include details of the sample size, inspection criteria, inspection methods, and the results of the inspection, including any defects that were detected.
Advantages of IQC Inspection
Â
IQC inspection provides a number of benefits, including:
Â
Â
Early detection of defects:
Â
Detecting defects early in the production process, IQC inspection allows organizations to take corrective action before the defects become more significant and more costly to rectify.
Â
Â
Reduced scrap and rework:
Â
By detecting and correcting defects early, IQC inspection can help to reduce the amount of scrap and rework required, which in turn can help to lower costs.
Â
Â
Improved supplier quality:
Working closely with suppliers helps ensure that the materials and components they supply meet the required standards, IQC inspection can help to improve supplier quality over time.
Â
Â
Increased customer satisfaction:
By producing high-quality products, IQC inspection can also help increase customer satisfaction and build a positive reputation for the organization.
Challenges in IQC Inspection
Â
Despite the many benefits, IQC inspection can present a number of challenges, including:
Â
Â
- Limited resources: Conducting IQC inspection can be time-consuming and resource-intensive, and organizations may not have the resources to devote to the process.
- Managing supplier non-compliance: Some suppliers may not be willing or able to meet the required standards, which can lead to non-compliance and quality issues.
- Balancing cost and quality: Organizations may struggle to balance the cost of IQC inspection with the need to maintain high standards of product quality.
- Keeping up with changing industry standards: The standards and regulations governing IQC inspection can change over time, and organizations may struggle to stay current and ensure compliance.
Conclusion
Â
IQC inspection is an important tool for ensuring product quality and minimizing the risks associated with producing defective products. Adopting best practices and staying current with industry standards can help organizations to maximize the benefits of IQC inspection while minimizing the challenges. By implementing IQC inspection in an effective and efficient manner, organizations can ensure that their products meet the required standards, increase customer satisfaction, and build a positive reputation for the organization.
Â
Â
If you need assistance conducting an IQC Inspection, Tetra Inspection can help you. As a global third-party quality control inspection services provider, we have the resources and experience and expertise to help in every step of the way.
Â
Â
Get in touch with us today to learn more.