For manufacturers, importers, and brands, acquiring robust equipment is fundamental to success. But when it comes to complex machinery, simply purchasing the latest and greatest isn’t enough. Guaranteeing the equipment’s functionality, efficiency, and safety demands a proactive approach, where due diligence reigns supreme. This is where the Factory Acceptance Test (FAT) steps in, acting as a critical checkpoint before your machinery leaves the factory floor.
What Is the Factory Acceptance Test?
Your shipment of machineries just arrived. But upon unpacking, questions remain. Does it truly meet your exacting specifications? Can it handle the demands of your operations? Will it integrate seamlessly with your existing infrastructure? These are anxieties the FAT alleviates.
Essentially, a FAT is a series of thorough tests conducted by the manufacturer, at their facility, before the equipment gets shipped to you. It comprises comprehensive quality checks, simulating real-world operating conditions and testing for potential failure modes. This proactive approach identifies issues before they become costly headaches at your site, saving you time, money, and frustration.
Why a Factory Acceptance Test (FAT) is Required
There are several key reasons why a Factory Acceptance Test (FAT) is required for industrial equipment and systems:
Early Problem Detection:
- Catch defects early: Identifying potential issues before the equipment is shipped saves you time, money, and hassle. Fixing problems at your site can be ten times more expensive than addressing them during the FAT.
- Prevent costly downtime: By uncovering potential malfunctions or performance inconsistencies early, you can prevent costly production downtime and avoid the disruptions caused by equipment failure after installation.
Contractual Assurance:
- Verify compliance: The FAT acts as a concrete proof point that the manufacturer has met your contractual obligations. It ensures the equipment meets all agreed-upon specifications, performance metrics, and safety standards.
- Reduce risk of disputes: A successful FAT minimizes the risk of contractual disputes by providing clear documentation and verification that the equipment meets your expectations.
Improved Installation and Commissioning:
- Smooth transition: A successfully passed FAT paves the way for a smoother and less error-prone installation and commissioning process. You can expect fewer surprises and disruptions at your site, leading to faster operational readiness.
- Reduce installation costs: By minimizing the need for post-installation troubleshooting and adjustments, the FAT can help lower your installation costs.
Enhanced Safety and Quality:
- Minimize safety hazards: Rigorous safety tests during the FAT ensure the equipment adheres to all relevant safety regulations and standards, minimizing the risk of accidents or injuries.
- Guarantee quality and performance: The FAT provides a comprehensive assessment of the equipment’s quality and performance, ensuring it meets your specific needs and expectations.
Building Trust and Confidence:
- Transparent communication: The FAT process fosters transparency and open communication between you and the manufacturer, building trust and confidence in your partnership.
- Peace of mind: Knowing your equipment has undergone a thorough testing and verification process provides peace of mind and reduces the anxiety associated with new equipment integration.
Factory Acceptance Test Checklist: A Comprehensive Guide for Manufacturers and Buyers
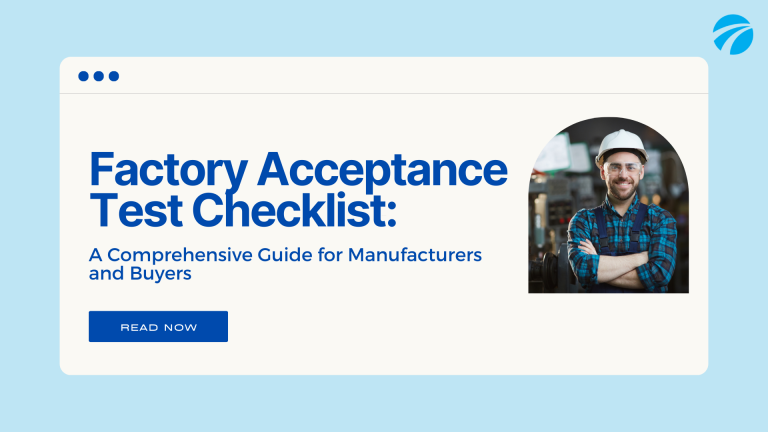
A comprehensive Factory Acceptance Test (FAT) checklist is crucial for ensuring the smooth and successful handover of industrial equipment from manufacturer to buyer. It serves as a roadmap for the testing process, guaranteeing all critical aspects are verified and documented. Here’s a detailed fchecklist you can adapt based on your specific equipment and requirements:
Pre-Inspection Preparation:
- Review Purchase Order and Specifications: Confirm the agreed-upon specifications, functionalities, and performance metrics for the equipment.
- Gather Documentation: Assemble all relevant documents like drawings, data sheets, certifications, factory inspection plans, and safety procedures.
- Schedule and Confirm Participants: Define the participants involved in the FAT, including manufacturer personnel, inspectors, and buyer representatives.
- Prepare Test Equipment and Instrumentation: Ensure all necessary tools, gauges, and measurement equipment are calibrated and available.
- Review Risk Assessment and Safety Measures: Familiarize yourself with potential hazards and ensure safety protocols are in place.
Visual Inspection:
- Overall Appearance: Verify the equipment matches the approved drawings and specifications for physical dimensions, components, and materials.
- Construction Quality: Check for weld integrity, paint finish, surface imperfections, and proper assembly.
- Cleanliness and Contamination: Ensure the equipment is clean, free of debris, and meets cleanroom requirements (if applicable).
- Labeling and Identification: Confirm all components are clearly labeled and numbered according to specifications.
- Safety Devices and Guards: Verify proper installation and functionality of safety features like guards, interlocks, and emergency stops.
Functional Testing:
- Individual Component Testing: Test each individual component and sub-system for proper operation and performance as per specifications.
- Operational Sequence Testing: Verify the equipment follows the designed operational sequence smoothly and seamlessly.
- Performance Testing: Push the equipment to its limits under simulated operating conditions to assess its capacity and performance against agreed-upon metrics.
- Control System Functionality: Test the control system’s functionality, accuracy, and responsiveness to commands.
- Alarm and Monitoring System Testing: Trigger alarms and test the functionality of monitoring systems for timely alerts and data recording.
Safety and Compliance Testing:
- Electrical Safety: Verify proper grounding, wiring, and compliance with electrical safety regulations.
- Mechanical Safety: Check for pinch points, sharp edges, and potential mechanical hazards.
- Environmental Testing: If applicable, perform tests for temperature, humidity, vibration, and other environmental factors the equipment might encounter.
- Noise Emission Testing: Measure and document noise levels emitted by the equipment to ensure compliance with regulations.
Documentation and Reporting:
- Record Test Results: Document all test observations, measurements, and deviations from specifications for each testing phase.
- Take Photos and Videos: Capture visual evidence of the testing process and any identified issues.
- Generate Detailed FAT Report: Compile all test results, observations, and photos into a comprehensive report with clear conclusions and recommendations.
- Review and Address Corrective Actions: Discuss identified issues with the manufacturer and define corrective actions before shipment.
Factory Acceptance Test Standards
While not a single, universal standard governs Factory Acceptance Tests (FATs), several industry-recognized standards and guidelines shape best practices and ensure quality, safety, and compliance. Here’s a closer look at three crucial standards:
ISO 9001 – Quality Management Systems:
- Foundation for Quality: This comprehensive standard establishes a framework for quality management across all aspects of an organization’s operations, including FATs
Key Requirements for FATs:
- Clear documentation of FAT procedures and expectations.
- Controlled testing environment with calibrated equipment.
- Traceability of test results for thorough documentation.
- Corrective actions for identified defects.
- Continuous improvement of FAT processes.
IEC6oo68 – Environmental Testing
- Ensuring Environmental Resilience: This standard specifies test methods for assessing equipment’s ability to withstand various environmental conditions, often included in FATs.
- Common Tests Covered:
- Temperature and humidity extremes
- Vibration and shock resistance
- Corrosive atmospheres
- Sand and dust exposure
- Other relevant environmental factors
IEC 61010 – Safety Requirements for Electrical Equipment:
- Protecting Personnel and Property: This standard focuses on electrical safety requirements for equipment, ensuring protection against electrical hazards during FATs and subsequent operation.
- Key Safety Aspects Addressed:
- Grounding and insulation
- Protection against electrical shocks
- Fire and explosion prevention
- Electromagnetic compatibility
Additional Considerations:
- Industry-Specific Standards: Alongside these general standards, certain industries often have additional standards or guidelines for FATs, tailored to their specific equipment and risks.
- Contractual Requirements: Specific FAT requirements and standards might be stipulated in contracts between manufacturers and buyers, ensuring alignment with their quality and safety expectations.
Tetra Inspection: Your Partner for a Smooth Factory Acceptance Test
Streamline your Factory Acceptance Test (FAT) with Tetra Inspection’s expertise. Our seasoned engineers and inspectors ensure a thorough and efficient process, minimizing risks and maximizing your equipment’s performance. Here’s how we help:
- Experienced FAT specialists: We understand the nuances of various equipment types and testing protocols, ensuring comprehensive coverage.
- Global reach and flexibility: We operate across the globe, readily available to conduct FATs at your convenience.
- Rigorous testing and reporting: We follow industry standards and customize tests to your specific needs, providing detailed reports for clear decision-making.
- Proactive problem identification: Our keen eyes and expertise catch potential issues early, preventing costly delays and post-installation headaches.
- Smooth communication and collaboration: We keep you informed throughout the FAT process, fostering trust and ensuring alignment with your expectations.
Partner with Tetra Inspection for a stress-free FAT and a confident equipment handover. Contact us today for a customized consultation!