How to Prepare for an ISO 9001 Certification
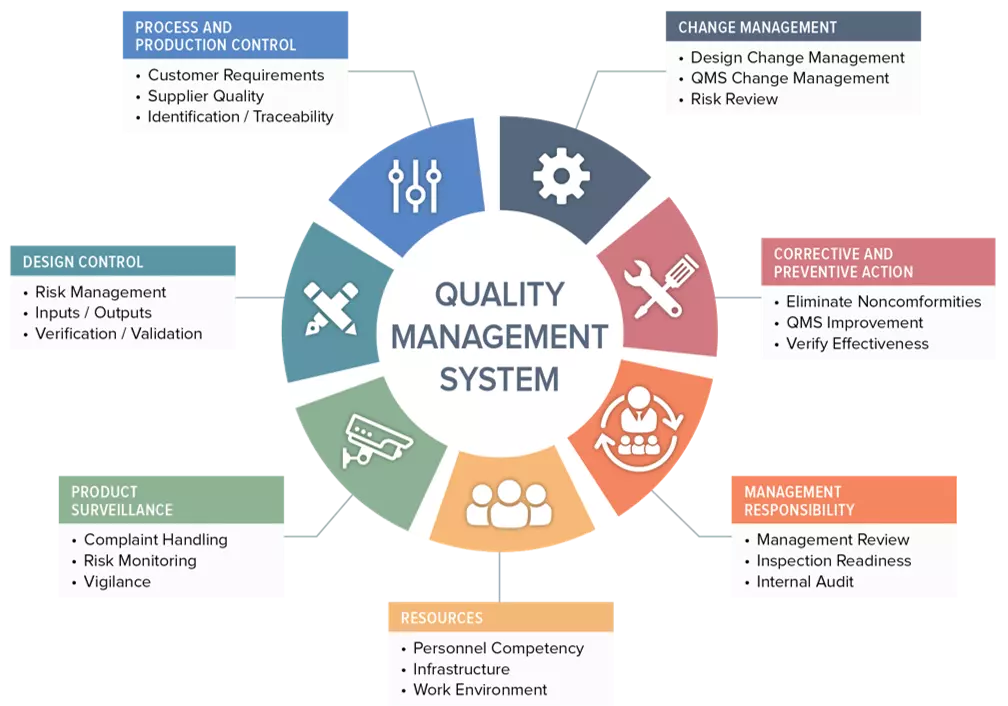
What is ISO 9001 Certification?
An ISO 9001 certification means that your company complies with the highest standard of manufacturing principles to deliver your product to your client at the highest satisfaction. In simple terms, it is the highest international standard for any production, service-orientated business. ISO 9001 standards are aimed at getting your management protocols at their absolute best. That means your clients get the best products and services from your company and that your management systems compare with the best.
ISO 9001 certification is all about your management processes and style. The 9001 standard applies to Quality Management Systems and not your products. Being ISO 9001 certified means that your business uses the highest quality systems and processes when it comes to managing your production or services.
It also requires you to have a constant improvement process. This means that your business must focus on continual improvement within these systems and processes.
Where to Start
To get certified in ISO 9001, you need to start by implementing the QMS within your company. There are many providers out there that will bid to facilitate this process for you. But if you follow this simple guide you will not only save yourself some money. But you will gain in-depth knowledge about how the ISO 9001 processes work and your business will be all the better for it. To start the process you need to follow these steps:
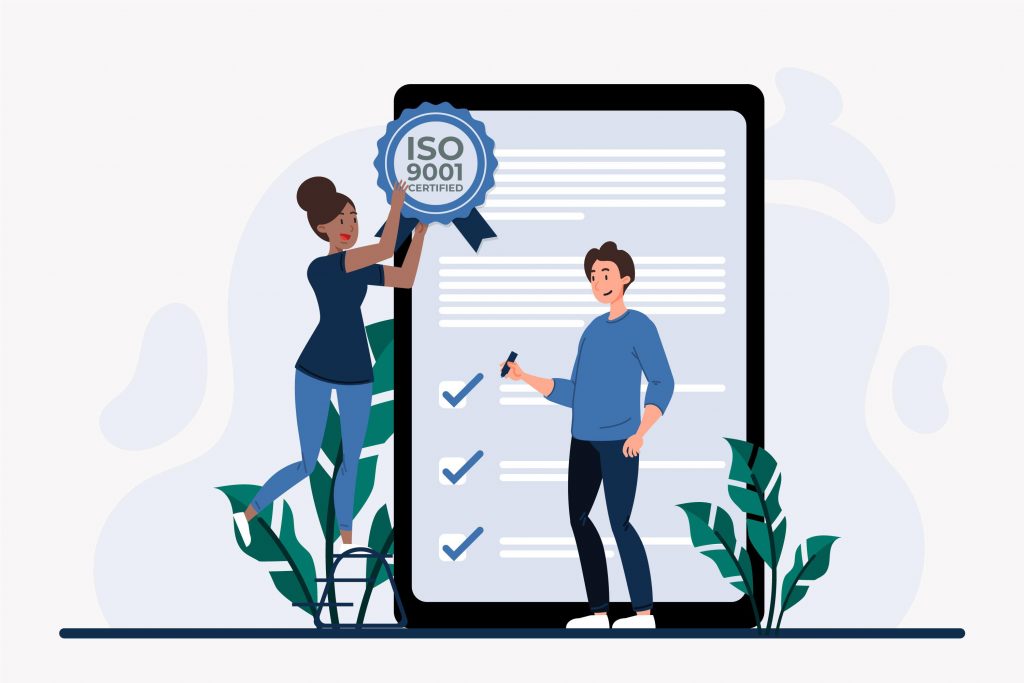
- Get acquainted with ISO 9001: To say that there is a mountain of literature on ISO 9001 certification is an understatement. However, QMS is a recognized management process and you will do well to read and study the material for your industry. Whether you get it online or offline it will only serve you well throughout this process.
- Plan your Implementation: This involves getting the right people to implement the management systems in your organization. QMS is a process that needs buy-in from the whole company, top to bottom. So you need to create an implementation plan that will require each person in your company to raise the standard to the ISO 9001 standard.
- Identify Objectives, Policies, and Responsibilities: As mentioned before ISO 9001 is an international standard for the management process. These processes will determine the quality of the products or services that your client will enjoy. So once you have created an implementation plan, you should use the QMS principles to identify the policies and processes that need to adjust to meet the standard. This will take you some time so remember don’t rush this process.
- Document Everything: Part of this certification process is the documentation that will guide your current staff and new employees. Maintaining your quality control is the most important part of your ISO 9001 certification preparation and certification. You need to compile the management documentation so that the auditor can inspect them at any time. Likewise, they need to be able to see the responses and rectifications that you have planned for any eventuality.
- Begin your Implementation: Once you have studied the literature, created your implementation plan, and documented the process, you are ready to start the implementation. This is the biggest step of all. This is where you see if your planning will deliver the goods. You will have to train your entire staff complement on the QMS and help them integrate it into their daily work schedules. You will start seeing the results of your planning and procedures within weeks of implementing the QMS.
- Review the Performance: In preparation for your certification, you need to get acquainted with the review process. Once you have implemented the process you need to review the progress regularly. We suggest that you start with a review every 2 weeks for the first 2 months. Thereafter you can review your progress monthly until you have secured the certification. Thereafter you will review the QMS process as per the stipulations in the ISO 9001 guidelines.
- Register for Certification: Once your implementation has been completed and you are confident that you can present a sufficient QMS process in your organization. You must register with your local ISO 9001 authority and request a registered auditor to come and review your hard work. The review process will involve the auditor going through all your documentation and resolution processes. Much the same as you have been doing until now. For a pre-audit, you can request a “trial run” audit where the auditor will review your documentation and offer you advice on any areas that might be lacking.
- Constant Improvement and Review: ISO 9001 certification is not a do it once exercise. It involves your organization constantly reviewing your QMS process and updating your systems and procedures on an ongoing basis. This will not only help you during the certification process but will also help to keep you on point with any developments in your business.
Final Audit for Certification Process
Before the final audit, there are a few things that you should know. Firstly you don’t have to go it alone. You can contract an ISO 9001 consultant to assist you with the implementation process. These consultants are up to date with the latest details on the auditing process as well as what you need for the certification process. The certification path could look anything like the below examples:
- Internal Implementation – this is where you do everything yourself. This approach might be low in cost to the company, but it requires you to do all the work yourself. That in itself is not a deterrent as your staff will learn more about the process than any other method. Because your team will be learning and creating as they go along the depth of knowledge gained is often far more than doing it any other way. This might also take longer than the other methods.
-
ISO 9001 Consultant, In-House: Hiring a consultant to work with your team in-house to achieve certification is often seen as the fastest way to get the process completed. However, there are some aspects that you should keep in mind. Firstly you should understand that although you will complete the process rapidly, you might not have as much internal ownership of the QMS process. This could cause some issues after completion as you will be wholly responsible for the sustainability of the system. Lack of ownership might result in failures and integration issues later on.
- ISO 9001 Consultant, Hands-Off: Considered the most expensive way of doing the certification, it does however have certain positive aspects. With an external consultant, your team will have more buy-in regards the internalization of the process. The staff will have to put in the time during the integration and implementation which will get you significant ownership of the process. Experienced external consultants will be able to improve your internal processes to achieve your certification.
- Registered ISO 9001 Certification KitThis method offers your organization 2 vital aspects for your certification. Firstly, it gives you a lower cost to implement as these kits are not very costly but have a huge amount of information within. Secondly, your team will not need to spend huge amounts of time developing internal processes and procedures as the kits will have easy-to-understand guidelines on how to set them up. This wi\ll cut down the time to implementation and ultimately the final certification. A positive of the certification kits is that your team does not need to have any prior experience with any of these systems or processes. So you can get the job done no matter the size or experience of your team. It just takes a little effort.
Also read:
- Certificate of Conformity: Why It Matters When Importing Goods?
- ISO 14001 Implementation: A comprehensive Guide
- G-Mark Certification Process Explained
Conclusion
Achieving an ISO 9001 certification is a commitment by your company to service excellence and superior management systems and procedures. It will elevate your business to a new level of customer experience that will ultimately reward you with higher revenue. That is of course if you sustain the system and follow the guideline as set out above. In truth, the certification itself does not make your business better. But it is the constant review and correction of any problematic areas within your business that makes your company shine brighter than your competition. ISO 9001 is a constant commitment to superior internal systems and management styles. So when you go through the process make sure that you have the best team behind you. That is the only surefire way to success.
How can Tetra Inspection help?
With our factory audit services centering on the core Quality Management Principles, we will help you audit your suppliers. These principles cover the 7 main areas where you can improve your ISO 9001 certification process and continue the excellent work in your facilities. These principles are:
- Customer focus
- Leadership
- Engagement of people
- Process approach
- Improvement
- Evidence-based decision making
- Relationship management
Get in contact with Tetra Inspection today and we will help you get your ISO 9001 certification done right. Tetra Inspection is the leading Quality Assurance inspector in the industry and you can rely on our superior staff. Review our services on Tetra Inspection.