As an importer or someone who outsources products from abroad, you may have to rely heavily on your suppliers to provide quality products that meet your standards. However, dealing with quality issues from suppliers is a common product compliance issues that can have a significant impact on your business. In this article, we will provide useful tips and strategies to help you effectively handle common quality management issues from your suppliers.
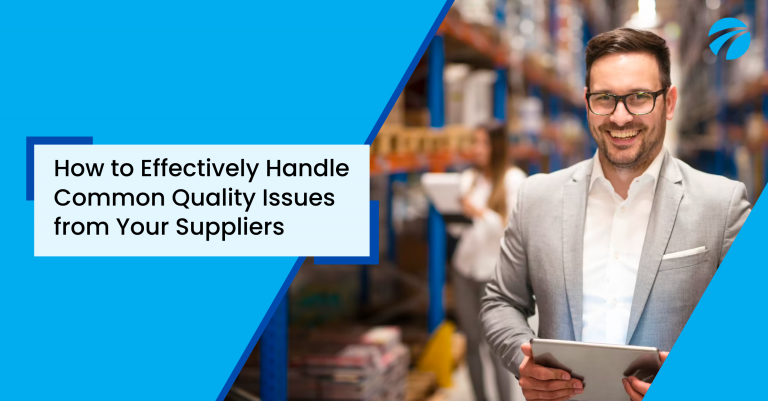
Clearly Define Your Quality Standards and AQL Limits
To avoid recurring quality issues, it’s essential to set clear quality standards and communicate them effectively to your suppliers. This involves defining your expectations for product quality, performance, and reliability, as well as specifying any testing requirements or performance criteria. To ensure that your suppliers are meeting your quality standards, it is essential to establish quality standards and AQL limits. AQL stands for Acceptable Quality Level and refers to the maximum number of defects or nonconformities that are acceptable in a batch of products. Here are some tips for setting quality standards and AQL limits:
Â
- Conduct a risk assessment to identify the critical quality attributes that are most important to your product.
- Set clear quality standards and communicate them to your suppliers.
- Establish AQL limits based on the critical quality attributes and the level of risk associated with the product.
Common quality issues from suppliers include:
Â
- Inconsistent product quality
- Poor packaging and labeling
- Shipping and logistics issues
- Incorrect product specifications
- Poor communication
- Delayed deliveries
- Non-compliance with quality standards and regulations
If you are experiencing any of these issues, it is crucial to take action quickly to minimize the impact on your business.
Conduct Regular Supplier Audits
Conducting supplier audits is an effective way to identify and address recurring quality issues. Performing audits on your suppliers allows you to gain a comprehensive understanding of their quality management systems, manufacturing processes, and product testing procedures. This helps you to identify any weaknesses in their processes that may be contributing to recurring quality issues. The earlier you can identify the quality issues and give feedback to your supplier, the lesser your chance of receiving defective and non-compliant products will be.Â
Communicate Quality Issues to Suppliers Early On
Â
Once you have identified a quality issue, the next step is to communicate it to your supplier. Effective communication is critical in ensuring that the supplier understands the issue and takes corrective action. Here are some tips to help you communicate quality issues to your suppliers:
Â
Â
- Clearly describe the quality issue and provide evidence to support your claim.
- Use a template to ensure consistency in your communication.
- Establish a corrective action plan that outlines the steps the supplier needs to take to resolve the issue.
- Avoid blaming or accusing the supplier and instead focus on finding a solution together.
- Set a deadline for the supplier to respond and take corrective action.
- Implement a preventive action plan to prevent the issue from recurring.
- Set clear expectations for future deliveries and quality standards.
Implement Supplier Scorecards
Implementing supplier scorecards is an effective way to track your suppliers’ performance and identify potential quality issues. Supplier scorecards typically include metrics such as;
Â
Â
- Delivery performance
- Product Quality
- Compliance with quality standards and regulations
- Responsiveness and communication
- Cost
Measuring supplier performance allows you to identify areas where the supplier is excelling and areas where they need to improve. If quality issues keep on happening, it’s also a good idea to investigate if your supplier is working with a sub-supplier. Regardless, if the quality issues persist, you may need to find an alternative to your current supplier.
Partner with a third-party inspection company
Partnering with a third-party inspection company like Tetra Inspection can help you combat recurring quality issues from your suppliers.
Â
Our highly qualified inspectors are well-versed with the latest quality standards and compliance and can help you identify potential quality issues before they occur. We’re currently operating in 40 countries across Asia, Africa Europe, and Latin America and have the shortest turnaround time of 24 hours. If you are looking for a global third-party inspection company, Tetra Inspection is the name you can trust.
Â
In conclusion, Handling quality issues from suppliers can be a challenging task, but by following the tips and strategies outlined in this article, you can effectively manage quality issues and minimize the impact on your business. Remember to establish clear communication with your suppliers, set quality standards and AQL limits, and measure supplier performance regularly. By taking a proactive approach to managing quality issues, you can ensure that your products meet your standards and exceed your customers’ expectations.