Piece by piece inspection China: How to choose the best Inspection agency
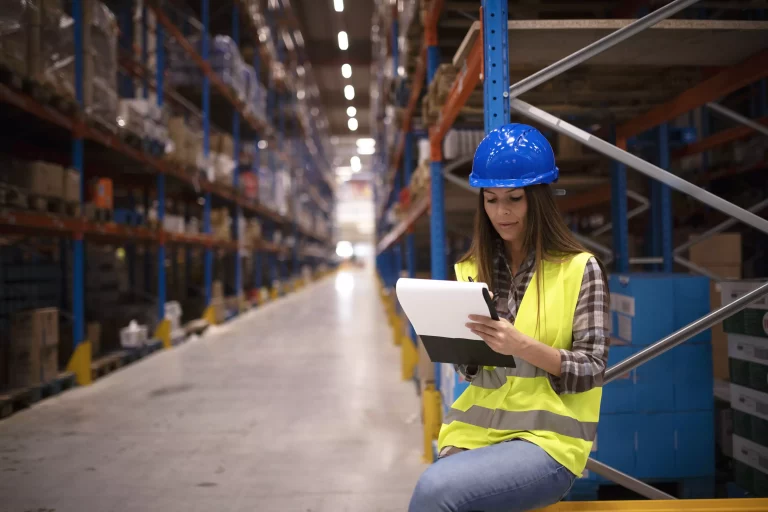
Piece by piece inspection is a quality assurance process in which each individual piece of a product is inspected for defects before shipment.  Because this particular type of QC inspections can be time-consuming, it is often performed at the end of the manufacturing process. This allows for any defective goods to be identified, reworked or replaced before the product is shipped.Â
Â
Piece by piece inspection China can be performed manually or using automated machines. When performed manually, a quality inspector will visually check each piece to eliminate defects to confirm defect free shipments. If a defect is found, the piece will be set aside and the next piece will be inspected. Automated piece by piece inspection machines uses sensors to check for defects. These machines can be programmed to stop the assembly process if a defect is detected.
Why do you need a piece by piece inspection in china?
When you are importing goods from China, a piece by piece inspection is very important in order to ensure that you are receiving exactly what you ordered.Â
Manufacturers in China often resort to cost-cutting measures that result in substandard products. This is why it’s important to inspect each individual piece of the shipment to make that it conforms to specified quality requirements.Â
There are a few different reasons why this type of inspection is so important. First, it allows you to eliminate defects or quality problems with the merchandise before it leaves the supplier’s facility. This can save you a lot of time and money, as you will not have to deal with returns or replacements once the goods arrive at your destination.
Second, a piece by piece inspection gives you a chance to check the accuracy of the packing list. This is important because it can help you avoid receiving short shipments or incorrect items.
Finally, this type of inspection allows you to verify the quantity of goods that you are receiving. This is especially important for larger orders, as you want to make sure that you are not being overcharged for the merchandise.
Advantages and disadvantages of a piece by piece inspection
Â
Â
Â
Conducting a thorough quality control inspection is crucial to ensuring that your products meet the highest standards. However, there are some drawbacks to this process that you should be aware of.
Advantages:
- Lowers the risks of receiving defective products
- Reduces product return rate
- Allows time to rework the defective productsÂ
- Saves money in the long run
- Ensures improved customer relations
Disadvantages:
- Piece by piece inspection is more expensive than Final Random Inspections (FRI)
- It’s more time-consuming than other types of inspections
- It increases the cost per unit without bringing any change to the product value
Difference between Piece by piece inspection and Final Random Inspection
A final random inspection is the last stage of inspection where products are randomly checked for quality standards. And because it’s a statistical process, it can miss defects that occur infrequently.
Â
Â
On the flip side, piece by piece inspection allows you to thoroughly examine every unit in a shipment and find all the defects. This makes it a more reliable method for ensuring quality, but it can be costly and time-consuming if you have a large number of units to inspect.
Piece by piece inspection China: How to prepare for it
Â
Â
If you are an importer working with a Chinese supplier, make sure to prepare for a quality control inspection in advance to avoid any last-minute surprises. Here are a few tips to help you get started:
Â
Â
Random Quality Inspection:
Have your products sampled and inspected by third-party quality control services in China. Follow the AQL (Acceptable Quality Level) sampling procedure to determine how many units they should be pulling per lot.
Â
Check the conformity of the product to your specifications:
Conduct a thorough inspection of your products and match them against the specifications. This includes but is not limited to;
Â
- Dimensions
- Functionality,
- Tolerances
- Materials
- Finishes, etc.
Labelling, marking and packaging requirements:
Â
Â
Make sure to check the accuracy of the labelling, marking and packaging requirements before the goods are shipped. If your goods were opened during the inspection, make sure that they were properly repacked before the shipment. In addition to that, make sure the manufacturer used the right packaging materials. This will prevent any kind of damage to your products during transportation.
Â
Identify, categorize and report the defects:
The quality control company should provide you with a detailed inspection report outlining their findings. They should also categorize the defects into three categories;
Â
Â
Minor Defect:
A minor defect is a cosmetic issue that does not affect the functionality of the product.
Example of a minor defect: An uncut thread on a garment.
Â
Â
Major Defect:
A major defect is a more serious issue that could affect the performance of the product.
Example of a Major Defect: Laptop batteries getting overheated.
Â
Critical Defect:
A critical defect is a flaw that makes the product unsafe for use.
Example: A sharp edge on a toy that might injure a toddler while playing.
Â
An ideal inspection report comes with photos/videos and complete test results (if applicable). This document will detail all the findings of the inspection and can be used as evidence later on if there are any disputes with the supplier.
Â
Â
Perform onsite/offsite testing:Â
Onsite testing is conducted at the manufacturer’s premises, while offsite testing is done at a third-party inspection lab or warehouse.
Â
Some of the most common tests used for quality control inspections are:
Â
Â
- Visual Inspection: This is a basic inspection where the inspector looks for any visual defects.
- Functional Testing: A functional test determines if the product is functioning as intended.
- Durability Testing: This test is used to check how well the product can withstand wear and tear.
- Material Testing:Â A material test helps determine the quality of the materials used in the product.
- Safety Testing: By conducting a safety test, an inspector examines and verifies if the product is safe for use.
Quality control inspections services by Tetra Inspection:
Tetra Inspection is one of the world’s leading inspection, verification, testing and certification companies. We are recognized as the global benchmark for providing high-end customized quality inspections services at any production phase.Â
Â
Â
We hire and retain only the best-in-business quality inspectors, auditors and business managers to provide a tailor-made quality control solution for you. Operating in 40 countries, our 350+ inspectors and auditors have unrivalled experience across a wide range of product categories: Softlines, Hardlines, Electronics, and Toys.
Â
Â
From Initial Production Check to Final inspection and everything in between, we have the expertise and resources to ensure that your products meet the highest quality level you paid for.Â
Â
Contact us today to learn more about how we can help you protect your brand, reputation and supply chain with our comprehensive quality control inspections services.
Â
Conclusion
Inspections can be time-consuming, and if not done properly, can result in a lot of wasted money and effort.Â
Â
A Piece by piece inspection is a vital quality control step that should be considered when manufacturing products in China. By taking the time to inspect each piece before assembly, you can ensure that your product meets your high standards and are compliant with all country and market quality requirements.