For any manufacturer, importer, or well-reputed brand outsourcing from abroad, a well-functioning, and predictive supply chain is the backbone of success. Yet, navigating the complexities, especially with new suppliers, introduces a range of risks. To tackle these challenges head-on, it’s essential to perform manufacturing audits or factory audits. In this guide, we’ll discuss everything about manufacturing audits, exploring their benefits and how Tetra Inspection can be a reliable partner in this crucial process.
What is a Manufacturing Audit?
A manufacturing audit is a systematic and thorough assessment of the manufacturing processes aimed at identifying and rectifying production quality issues. It encompasses a holistic assessment, including the manufacturer’s capacity, process, workplace environment, and capabilities. The primary goal of a manufacturing audit is to ensure that the manufacturer can produce goods according to specified requirements and legal standards.
Why Perform a Manufacturing Audit?
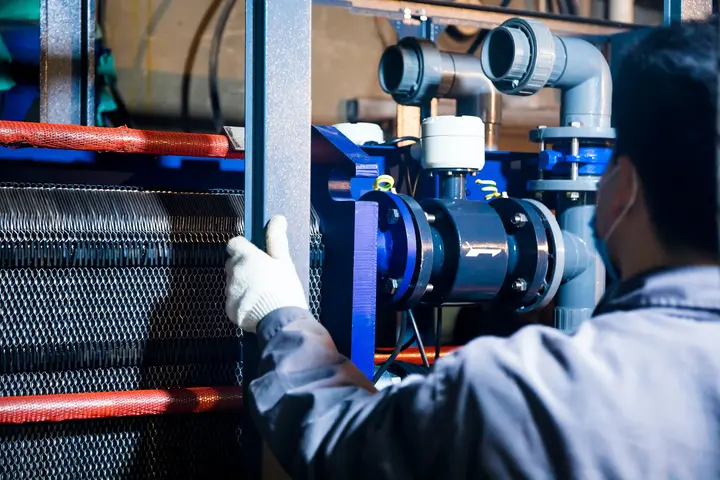
Manufacturing audits serve various purposes, ranging from assessing compliance with regulations to enhancing production processes and auditing new suppliers. The key benefits of a manufacturing audit include:
Â
Â
- Conducting a supplier verification audit to assess their capability for a specific project.
- Ensuring compliance with statutory and regulatory requirements.
- Providing a reliable assessment of the manufacturer’s capabilities and facilities.
- Offering an overview of the company’s processes, operations, and workflows.
- Identifying areas for improvement and implementing enhancements.
How is the Manufacturer Audit Conducted?
The process of conducting a manufacturing audit can vary based on the products involved and client specifications. However, a standard manufacturing audit includes:
Â
Internal vs. External Auditing
Manufacturer audits can be conducted either by an internal team within the company or by a third-party inspection company. The choice between the two depends on factors such as available resources, expertise, and the desired level of objectivity.Â
Â
Internal teams offer insider knowledge but may lack impartiality, while external auditors bring a fresh perspective and specialized skills.
Â
Audit Duration and Scope
The duration and scope of a manufacturer audit can vary based on the size of the business and the complexity of the manufacturing processes. Typically, audits range from one day to two weeks. It’s crucial to define the scope clearly, outlining the specific processes, departments, and areas that will be reviewed. This ensures a focused and efficient audit process.
Standard Manufacturer Audit Components
A standard manufacturer audit covers essential components that contribute to a holistic evaluation of the manufacturing capabilities. These components include:
Â
When conducting a manufacturing audit, a thorough examination of critical aspects is essential to ensure the reliability and capability of your suppliers.Â
Â
Here’s a concise breakdown of what to check during a manufacturing audit:
Â
Ownership of the Factory:
Verifying legal ownership of the factory allows you to avoid potential risks associated with undisclosed subcontracting. It ensures the supplier’s accountability and transparency in the manufacturing process.
Â
Legal Operating Status:
Confirming compliance with legal requirements ensures that the manufacturer operates within the prescribed regulations. This is crucial for maintaining ethical standards and avoiding legal complications.
Â
Facility Location:
Validating the reported location safeguards against misrepresentation. It ensures that the stated manufacturing site aligns with your expectations, preventing potential logistical and communication issues.
Â
Business Size:
Assessing the size of the business, including the number of employees, provides insights into the capacity and scalability of the manufacturer. This information is vital for aligning production capabilities with your specific requirements.
Â
General Production Capabilities:
Evaluating overall production capabilities is central to ensuring that the manufacturer possesses the necessary infrastructure and resources to meet your production needs. This step mitigates the risk of inadequate capacity.
Â
Facility Conditions:
It includes scrutinizing the physical condition of the facilities, including compliance with labor laws, ensures a safe and ethical working environment. It reflects a commitment to employee well-being and regulatory adherence.
Â
Production System Assessment:
Assessing the production system, including machinery, technical capabilities, and environmental controls, validates that the manufacturing processes align with industry standards. It guarantees product consistency and quality.
Â
Quality Control System Assessment:
Ensuring the presence of a robust quality control system is essential for maintaining product integrity. This step confirms that the manufacturer has established procedures in place to meet specified quality standards.
Â
Management Capabilities:
Evaluating management capabilities provides insights into the leadership’s ability to oversee and optimize production processes. Strong management is indicative of a well-organized and efficient operation.
Â
Financial Condition:
Scrutinizing the financial health of the business, including registered capital and credit grade, offers assurance of the manufacturer’s stability. Financial transparency is crucial for long-term partnerships.
Technical Manufacturing Audit
For a more in-depth assessment, a technical manufacturer audit goes beyond the standard components. It involves a detailed review and verification of:
Â
- Facility Conditions: Examining the physical condition of the facilities, including the structure, compliance with labor laws, and the overall working environment.
- Production Process Assessment: Assessing the production system, including working conditions, machinery, technical capabilities, and environmental control systems.
- Quality System Assessment: Ensuring a robust quality control system, including inspectors and adherence to quality control methodologies.
- Management Capabilities: Evaluating the management’s capabilities in overseeing and optimizing production processes.
- Financial Capabilities: Scrutinizing the financial health of the business, including registered capital and bank credit grade.
For a more detailed assessment, a technical manufacturing audit is conducted, which includes a department-by-department review covering aspects like facility conditions, production systems, quality control, and financial stability.
Manufacturing Process Audit Checklist
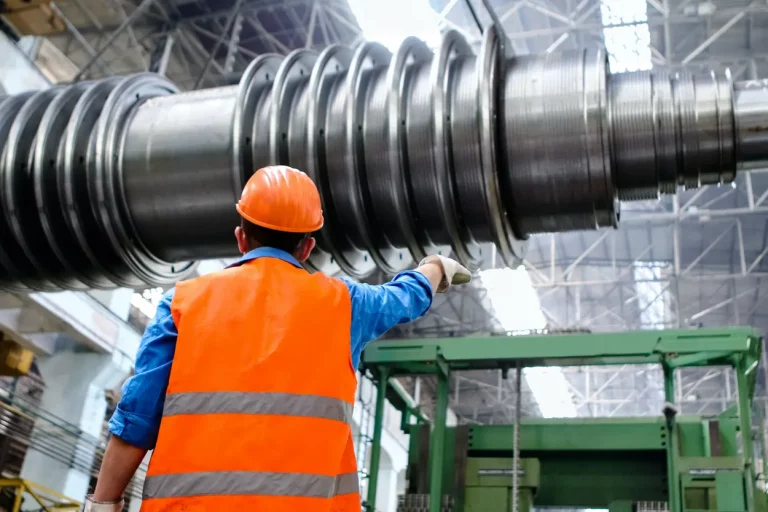
A well-planned manufacturing process audit is crucial for its success. Consider the following checklist:
Conducting a manufacturing process audit is a critical step to guarantee the efficiency and quality of production. To facilitate a comprehensive evaluation, utilize the following checklist, focusing on key aspects that contribute to seamless operations:
1. Define the Purpose:
Clearly define the objectives of the audit. Determine whether it aims to improve existing operations or address specific quality issues within the manufacturing process.
2. Select the Audit Team:
Choose a well-qualified audit team, either internal or a 3rd-party inspection company, to ensure a thorough and unbiased assessment. Consider expertise and experience in the industry.
3. Audit Frequency:
Decide whether the audit will be a one-time evaluation or a regular, ongoing process. Regular audits contribute to continuous improvement and sustained operational excellence.
4. Timetable Specification:
Clearly outline the audit timetable with detailed schedules. Ensure coverage of entire shifts and random observations to obtain a fair and accurate assessment.
5. Conduct the Audit According to Timetable:
Execute the audit as planned, covering all specified areas. Ensure that all relevant staff is informed about the audit process to facilitate a smooth evaluation.
6. Document Issues Discovered:
Thoroughly document any issues or discrepancies identified during the audit. Use this documentation as a basis for implementing future improvements and corrective actions.
7. Inform Stakeholders of Audit Results:
Communicate the outcomes of the audit to all relevant stakeholders, fostering transparency and providing an opportunity for input and suggestions.
8. Collect Feedback from Staff:
Allow staff and employees affected by the audit to offer feedback and suggestions for improvement. Inclusion promotes a collaborative approach to problem-solving.
9 Corrective Actions:
Determine the most effective corrective actions based on audit findings and stakeholder feedback. Address issues promptly and implement necessary improvements.
When is a Manufacturing Process Audit Required?
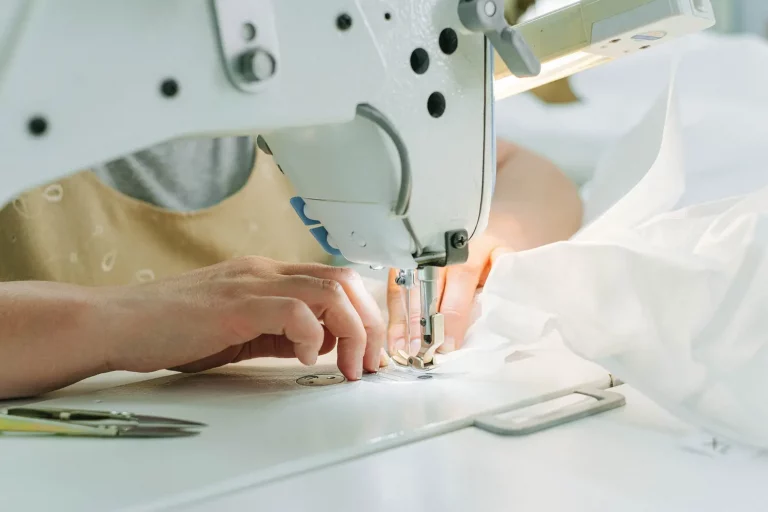
Conducting a manufacturing process audit is a strategic decision influenced by various factors. Knowing when to initiate this critical evaluation ensures proactive risk management and operational optimization.Â
Â
Here are scenarios indicating when a manufacturing process audit is required:
Â
Supplier Qualification:
Most companies have supplier onboarding processes. A manufacturing process audit is essential to assess a supplier’s capabilities before onboarding, ensuring they meet specific production requirements.
Â
Preproduction Validation:
Before mass production begins, conducting a thorough initial production inspection is essential. It identifies potential flaws, streamlines operations, and upholds regulatory compliance, preventing costly deviations from standards.
Â
Root Cause Analysis:
When quality issues arise, a manufacturing process audit is required to investigate the root cause of defects. This risk-based analysis helps identify production bottlenecks, sources of defects, and areas needing improvement.
Â
Â
Efficiency Gains:
Businesses seeking efficiency gains and resource optimization often utilize manufacturing process audits. These audits identify inefficiencies and bottlenecks, enabling targeted improvements.
Â
Large Orders or Technical Products:
For companies dealing with large orders or technically intensive products, a manufacturing process audit is crucial. It helps identify and mitigate specific production risks associated with complex manufacturing requirements.
Â
Change in Key Personnel or Processes:
Over time, changes in key personnel, equipment, or processes may impact product quality. Conducting a manufacturing process audit is required to ensure ongoing adherence to standards.
Â
Post-Quality Issues:
If there are signs of frequent quality issues, defective products returns, or customer complaints, a manufacturing process audit is required. This helps identify and address issues affecting product quality.
How Tetra Inspection Can Help
Tetra Inspection specializes in providing comprehensive manufacturing audit services tailored to your specific needs.Â
Our process audit framework covers technical documentation, quality control, process analysis, personnel and material resources, efficiency, and output.Â
Â
Our experienced auditors ensure a thorough assessment, offering insights into the risk profile of your production line and recommending areas for improvement.
Â
To learn more about our Manufacturing Audit, contact us today!