Garment quality control is the cornerstone of excellence in the fashion industry.
In a highly competitive market, where customer satisfaction and brand reputation are paramount, ensuring that garments meet the highest standards of quality is essential. From fabric sourcing to final inspections, rigorous quality control measures play a vital role in delivering products that not only meet customer expectations but also adhere to international standards and certifications.
In this article, we will explore the challenges faced in garment quality control, and discuss the best practices that ensure effective quality control, and discover how brands can navigate these complexities to maintain excellence and drive success in the dynamic world of fashion.
The Strategic Importance of Garment Quality Control in Fashion
Â
Garment quality control is crucial to maintaining a brand’s reputation and profitability in the fashion industry. It ensures that each product meets established standards from fabric sourcing through to the final inspection. By implementing stringent checks at every stage of production, brands can consistently deliver products that meet customer expectations and adhere to industry regulations.
Â
However, neglecting quality control can have serious consequences. Without proper oversight, defects may go unnoticed, leading to increased returns, dissatisfied customers, and a damaged brand image. Worse yet, these issues can escalate into larger problems, including product recalls. A recall not only costs the company in terms of logistics and lost revenue, but it also severely undermines consumer confidence in the brand. The impact of such recalls can linger, damaging customer loyalty and affecting future sales.
Â
Quality control isn’t just about preventing defects—it’s about protecting the brand’s integrity and ensuring that the products a company puts out into the market uphold its promise. A strong quality control system mitigates the risk of recalls and reduces costly production errors, ultimately safeguarding the business’s long-term success and consumer trust.
Â
Â
Key Components of Garment Quality Control
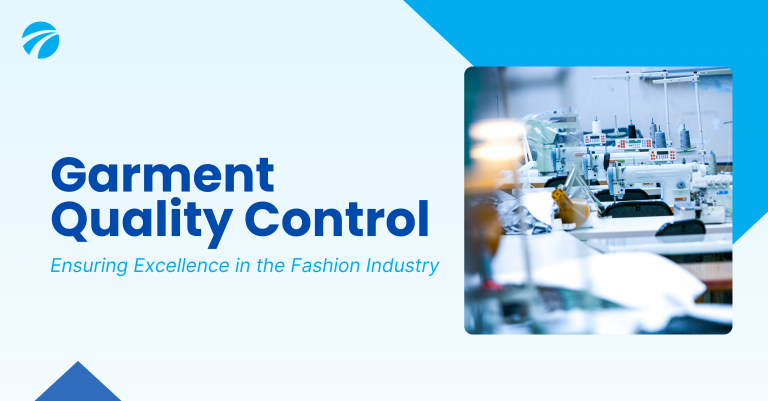
Quality Control Procedures
Fashion brands must adhere to strict quality control protocols at different stages of production. Before manufacturing begins, Pre-production inspections focus on ensuring the fabric, color, and prints meet the required standards. During the manufacturing process, in-line inspections are essential for monitoring quality on the shop floor. Any defects or inconsistencies are addressed promptly, ensuring smooth production flow. Finally, once production is complete, a thorough final inspection and product testing take place to ensure every garment meets the brand’s specifications and quality standards before being shipped.
Product Specification Compliance
Every garment must meet an array of strict product specifications, ranging from design and size to packaging and shipping standards. Compliance is crucial to ensure that each item matches the brand’s vision and customer expectations. Quality control teams verify that these specifications are consistently met throughout production. In cases where deviations from the set standards are found, corrective actions are taken quickly to prevent discrepancies that might affect the garment’s final appearance or functionality.
Defect Identification and Classification
Inspectors are trained to detect various types of defects that may arise during the production of garments. Defects can range from minor stitching issues to more significant flaws like faulty zippers, incorrect colors, or misaligned labels. These defects are then categorized based on their severity and potential impact on the garment’s overall quality. The use of acceptable quality levels (AQL) allows the brand to define the threshold for defects, ensuring that only garments that meet the required standards reach the market.
Statistical Quality Control Techniques
Fashion brands rely heavily on statistical quality control techniques to improve their production process. Using random sampling, a representative number of garments are selected for inspection. Data from these inspections is then analyzed to identify trends, recurring issues, or potential sources of defects. By applying statistical methods, brands can pinpoint the root causes of defects and implement measures to prevent them in future productions, creating a cycle of continuous improvement and refinement in manufacturing practices.
Benefits of Garment Quality Control
Cost Reduction and Efficiency
Implementing effective quality control measures can result in cost reduction and improved efficiency. By detecting and rectifying defects early in the production process, rework and waste can be minimized. Quality control also helps optimize production processes, reducing lead times and enhancing productivity. Streamlining operations and minimizing defects contribute to overall cost savings and improved profitability.
Compliance with Regulations and Standards
Garment quality control is essential for ensuring compliance with safety and quality regulations. The fashion industry is subject to various regulations regarding product safety, chemical usage, and environmental sustainability. Quality control helps brands meet these regulatory requirements, avoiding legal issues, penalties, and reputational damage. Additionally, adhering to international standards and certifications demonstrates a commitment to quality and responsible manufacturing practices.
Customer Satisfaction and Loyalty
Garment quality control directly impacts customer satisfaction and loyalty. By delivering high-quality products consistently, brands can meet customer expectations and build trust. Satisfied customers are more likely to become loyal brand advocates, leading to repeat purchases and positive word-of-mouth recommendations. Quality control ensures that garments meet the desired standards, reducing the risk of customer dissatisfaction, returns, and negative reviews.
Challenges in Garment Quality Control
Supply Chain Complexity
In the garment industry, it can be challenging to control the quality of clothes because the supply chain is complicated. There are many suppliers involved, and they may be located in different places. This can make it hard to make sure the clothes are made well. Language and cultural differences can also create problems in communicating about quality standards. The industry is also under a lot of pressure to make clothes quickly, which can lead to shortcuts in checking for quality. The clothes themselves can be complex, with lots of details and different fabric materials.
On top of that, some rules and standards need to be followed. Sometimes, parts of the production process are given to other companies, which makes it even harder to keep control over quality. To overcome these challenges, it’s important to have clear standards, good communication with suppliers, regular checks, and the right technology. Working together and being open with everyone in the supply chain is also key to making sure the clothes are of good quality.
Human Error
Human error poses a significant challenge in garment quality control during production. Factors such as fatigue, lack of training, miscommunication, carelessness, skill variations, and time pressure contribute to these errors. To overcome this challenge, garment manufacturers can implement quality control inspections. These inspections involve carefully checking garments at various stages of production to identify and rectify errors. By inspecting the garments, workers can catch mistakes like incorrect measurements, faulty stitching, or missed details before the final product is completed. Additionally, inspections help maintain consistency in quality by ensuring that all garments meet the established standards.
Time and Cost Constraints
Balancing quality control activities with production timelines can be challenging. There is a need to allocate sufficient time for inspections and testing without causing delays in the overall manufacturing process. Moreover, quality control activities require dedicated resources, which can impact production costs. Striking a balance between quality control and production efficiency is crucial to meet both customer expectations and business objectives.
Best Practices for Effective Garment Quality Control
Â
Supplier Evaluation and Selection
To ensure consistent textile quality, it is important to evaluate and select reliable suppliers. Assessing supplier capabilities, track record, and commitment to quality helps in making informed decisions. Clear quality requirements and expectations should be communicated to suppliers, establishing a collaborative approach to maintain high standards throughout the supply chain.
Â
Documentation and Standard Operating Procedures
Comprehensive documentation of quality control guidelines and standard operating procedures is essential for consistency and accountability. These documents provide a reference for inspectors and help maintain uniformity in quality evaluations. Standardized procedures ensure that inspections are conducted systematically and thoroughly, minimizing the risk of errors and deviations.
Â
Training and Skill Development
Investing in training programs for quality control personnel enhances their knowledge and skills. Training should cover quality control techniques, defect identification, classification, and data analysis. By equipping inspectors with the necessary expertise, brands can improve the accuracy and reliability of quality control processes.
Â
Collaboration and CommunicationÂ
Maintain open lines of communication with suppliers, production teams, and quality control personnel. Collaborate closely with suppliers to align quality requirements and expectations. Regularly communicate with production teams to ensure that they are aware of quality standards and requirements. Foster a culture of open communication within the organization, encouraging feedback and suggestions for improvement.
Â
Continuous ImprovementÂ
Strive for continuous improvement in garment quality control processes. Regularly evaluate the effectiveness of quality control measures and identify areas for enhancement. Encourage a culture of learning and innovation, where employees are empowered to suggest improvements and implement changes. Embrace industry best practices, stay updated with technological advancements, and seek customer feedback to drive continuous improvement.
Â
Garment Quality Control: How Tetra Inspection Can Help
As an esteemed global leader in the garment quality control industry, Tetra Inspection provides an extensive array of tailored solutions to cater to the distinct requirements of fashion brands across the globe. With our unwavering commitment to excellence, Tetra Inspection ensures that every garment adheres to the highest quality standards and complies with regulations.Â
Â
Our team of highly qualified inspectors, equipped with in-depth knowledge of industry regulations, conducts meticulous inspections at every stage of the manufacturing process.
Â
Utilizing a digital inspection dashboard, Tetra Inspection provides clients with real-time access to inspection reports, offering transparency and actionable insights.Â
Â
With a global presence spanning 40 countries, Tetra Inspection guarantees prompt delivery of inspection reports within 24 hours, enabling brands to make informed decisions swiftly.
Â
To learn more about our Garment Quality Control Services, contact us today!.
Â