Furniture Inspection - Furniture Quality Control Expertise
Furniture QC
Furniture Quality Control – Furniture Inspection expertise
Quality and safety are paramount in the furniture industry, and that’s where furniture inspection comes into play.
Avoid recalls, uphold your reputation, and ensure full compliance with Tetra Inspection’s comprehensive furniture inspection services. With our meticulous inspections, you’re assured of compliant, defect-free products every time. Entrust your brand to our team of highly qualified inspectors dedicated to quality, compliance, and protecting your bottom line.
Book a furniture inspection service today!
Understanding The Importance Of Furniture Inspection
Furniture inspection plays a pivotal role in the manufacturing and distribution process for furniture companies. It is crucial to ensure that the products meet quality standards, safety regulations, and customer expectations. Let’s explore why furniture inspection matters and its impact on various aspects of the business.
The Impact of Substandard Furniture on Customers
Upholding Brand Reputation and Trust
Avoiding Costly Recalls and Returns
Compliance with Standards and Safety Regulations
FURNITURE TESTING
Key Elements Of Furniture Testing
Furniture testing involves a thorough examination of various elements to ensure the quality, safety, and compliance of the products. Let’s explore the key elements that are commonly assessed during furniture testing:
- Material Quality Assessment
During furniture inspection, the materials used in the manufacturing process are carefully examined to verify their quality and suitability for the intended use. This assessment includes:
Â
- Wood and Wood-Based Materials:Â Inspecting the type of wood used, checking for knots, warping, and signs of damage.
- Upholstery and Fabrics:Â Assessing the fabric quality, stitching, and overall upholstery finish.
- Metal Components:Â Checking for rust, cracks, or sharp edges in metal parts of the furniture.
- Structural Integrity Checks
The structural stability and integrity of the furniture are critical to its safety and performance. The inspection includes:
Â
- Frame and Joint Stability:Â Ensuring that the frame is sturdy and joints are securely fastened.
- Load-Bearing Capacity:Â Verifying that the furniture can support the intended weight without failure.
- Fastener Strength:Â Checking the strength of screws, bolts, and other fasteners used in assembly.
- Finishing and Surface Evaluation
The finishing and surface quality of the furniture contribute to its overall aesthetics and durability. Inspection covers:
Â
- Surface Smoothness and Finish Consistency:Â Ensuring a smooth and uniform finish without rough spots or irregularities.
- Stain and Scratch Resistance:Â Testing the resistance of the surface to stains and scratches.
- Colorfastness and Fading:Â Verifying that the color of the furniture remains consistent and does not fade easily.
- Safety Features Assessment
For furniture designed for specific purposes, such as cribs or highchairs, safety features are essential. The inspection includes:
Â
- Safety Mechanisms:Â Checking the functionality of safety features, such as locks or latches.
- Edge and Corner Protection:Â Ensuring that sharp edges and corners are adequately covered or rounded.
- Assembly and Packaging Verification
Inspectors assess how well the furniture is assembled and packaged for shipping to prevent damages during transportation. This involves:
Â
- Assembly Quality:Â Verifying that the furniture is assembled correctly according to the provided instructions.
- Packaging Integrity:Â Ensuring that the packaging provides adequate protection during transit.
- Compliance with Quality Standards
- Functionality and Performance Testing
- Workmanship and Aesthetics
- Packaging and Labeling
Inspectors verify that the furniture is appropriately labeled with necessary information, such as care instructions and safety warnings, and that the packaging is labeled correctly for easy identification.
Â
Furniture inspection is a comprehensive process that considers these key elements to guarantee that the end products meet the desired quality standards and safety regulations, providing customers with furniture they can trust and rely on for years to come.
Furniture QC process
The Furniture Inspection Process
Furniture inspection is a vital step in the manufacturing and distribution of furniture products, designed to ensure that the items meet the required quality standards and safety regulations. It involves a systematic and thorough examination of various aspects of the furniture to identify any defects or issues that need to be addressed before the products reach the market. Let’s delve into the different stages of the furniture inspection process:
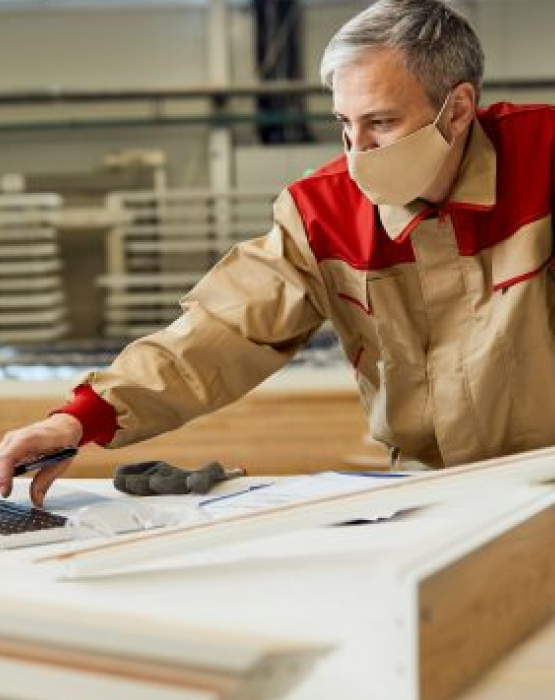
The first stage of the furniture inspection process takes place before the actual production begins. During Initial Production Inspection, inspectors work closely with manufacturers to review design specifications, verify material samples, and ensure that the factory has the capabilities to produce the furniture to the desired quality standards.
Â
Material Sampling and Verification:Â Inspectors collect samples of the materials that will be used in the furniture, such as wood, fabric, and metal, to verify their quality and suitability for the intended purpose.
Â
Reviewing Design Specifications:Â Inspectors thoroughly review the design specifications provided by the manufacturer to ensure that they align with the desired quality and safety requirements.
Â
Ensuring Factory Capabilities:Â The inspectors assess the factory’s production capabilities, equipment, and workforce to determine if they have the capacity to meet the production demands while maintaining quality.
The final inspection is conducted once the furniture production is completed and a batch of products is ready for shipment.
Â
Checking Finished Products:Â Inspectors randomly select samples from the batch and thoroughly examine them to ensure that they meet the desired quality standards and comply with safety regulations.
Â
Conducting Functionality Tests:Â The functionality of moving parts, such as drawers, hinges, or reclining mechanisms, is tested to verify smooth operation and functionality.
The final inspection is conducted once the furniture production is completed and a batch of products is ready for shipment.
Â
Checking Finished Products:Â Inspectors randomly select samples from the batch and thoroughly examine them to ensure that they meet the desired quality standards and comply with safety regulations.
Â
Conducting Functionality Tests:Â The functionality of moving parts, such as drawers, hinges, or reclining mechanisms, is tested to verify smooth operation and functionality.
During Container Loading Inspection, inspectors oversee the packaging process to ensure that the furniture is adequately protected for transportation and loaded correctly onto shipping containers.
Applicable Standards For Furniture Quality Control
Furniture quality control is essential to ensure that products meet the necessary safety and performance standards, providing customers with reliable and durable furniture. Various national and international standards govern furniture quality control, setting guidelines for materials, manufacturing processes, and overall product performance. Here are some highlighted points on applicable standards for furniture quality control:
Â
Â
- USA: ANSI/BIFMA standards –Â The American National Standards Institute (ANSI) and the Business and Institutional Furniture Manufacturers Association (BIFMA) have established comprehensive standards for office and institutional furniture. These standards cover factors such as structural integrity, stability, and ergonomics.
- European Union: EN standards –Â The European Committee for Standardization (CEN) has formulated EN standards that apply to a wide range of furniture products. These standards cover safety, strength, and performance requirements for indoor and outdoor furniture.
- International Organization for Standardization (ISO) standards –Â ISO has developed various standards related to furniture quality control. ISO 7173 specifies dimensions for chairs and seating, while ISO 7174 focuses on strength and durability testing. ISO 4892-2 deals with exposure to laboratory light sources for materials.
- ASTM International standards – ASTM develops voluntary consensus standards for a wide range of products, including furniture. ASTM F2057, for example, provides safety guidelines for clothing storage units.
These standards cover a wide range of aspects, including material specifications, structural integrity, surface finish, safety requirements, and performance testing. Adhering to these standards ensures that furniture products are safe, reliable, and compliant with industry best practices. Manufacturers, brands, and importers who prioritize furniture quality control based on these applicable standards can offer products that meet customer expectations, enhance brand reputation, and contribute to a positive and trustworthy market presence.
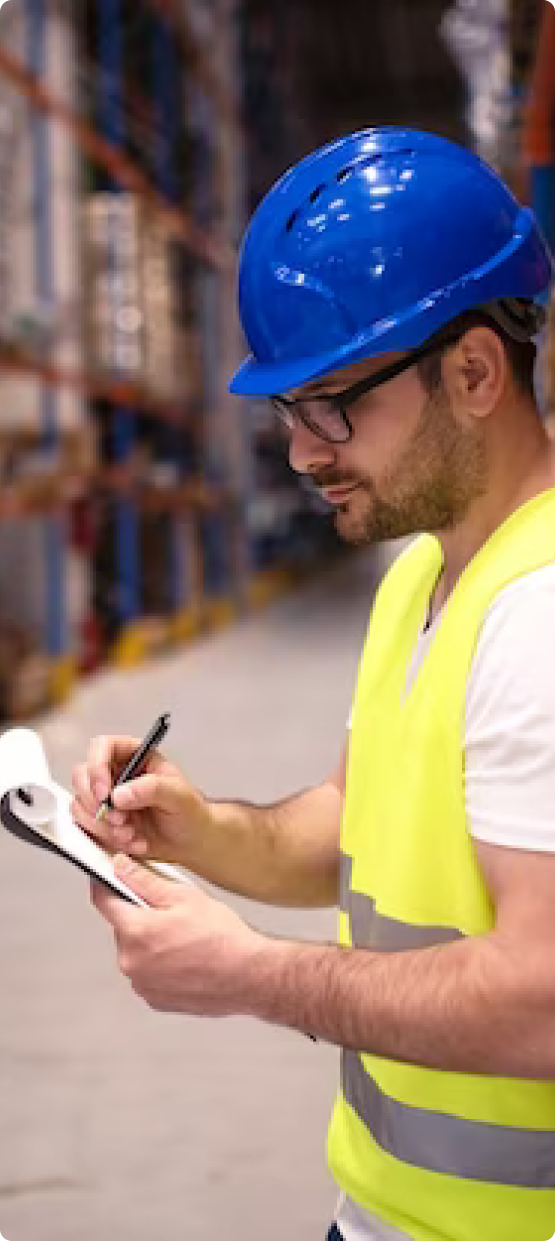
How Tetra Inspection Can Help With Furniture Quality Control
Comprehensive Inspections
Tetra Inspection conducts comprehensive pre-production, during production, and pre-shipment inspections, following the AQL standards, leaving no room for subpar products to slip through the cracks.
Detailed Reports With Digital Evidence
Our furniture Inspection report comes with digital evidence, enabling efficient identification, categorization of defects and recommendations. With Tetra Inspection, you can expect timely and detailed inspection reports, allowing you to take prompt action if any issues arise.
Customizable Solutions
Understanding that different companies have unique requirements, Tetra Inspection offers customizable inspection solutions that align with your specific quality standards.
Global Coverage
Tetra Inspection has a strong network of 350+ skilled inspectors located in 40 countries, catering to diverse clients and industries.
Schedule Your Furniture Inspection Today
Rely on our team of highly seasoned experts for meticulous furniture inspection, effectively minimizing risks and ensuring strict adherence to international standards.
Common Questions About Pre-Shipment Inspection, Answered (FAQ)​
The cost of a furniture inspection service depends on the pricing plan you opt for. Here are the plans we offer:
Â
Standard Rate:
Price: $240 per man-day
Â
Monthly Plan:
Price: $189 per man-day (over 20% savings) Billed Monthly at $1,899 for 10 furniture inspections across Asia
Â
Annual Plan (Recommended):
Price: $158 per man-day (over 35% savings) Billed Monthly at $1,584 for 120 furniture inspections across Asia (12 months subscription)
Furniture inspection is essential for manufacturers and importers to ensure that the furniture products they produce or source meet the required quality and safety standards. It helps prevent faulty or defective items from reaching the market and protects customers from potential hazards.
No, furniture inspections are essential for all types of furniture productions, regardless of scale. Whether you are a small-scale manufacturer or a large importer, inspections play a vital role in maintaining product quality.
Yes, thorough furniture inspections can significantly reduce the risk of product recalls. Identifying and rectifying defects before shipping prevents faulty products from entering the market and protects the brand’s reputation.
Importers often work with various suppliers and manufacturers, each with specific quality requirements. Tetra Inspection’s customizable solutions allow importers to adapt inspections to different suppliers and ensure consistency in product quality.
Tetra Inspection provides timely inspection reports within 24 hours of conducting the inspection. This allows businesses to take prompt action based on the findings.
Yes, Tetra Inspection offers on-site inspections for manufacturers located in different countries, ensuring that the products meet the required quality standards before shipment.
BLOG
Related Articles
shipment, minimizing risks and ensuring compliance with international standards.