Sneakers are a massive cultural force. They’re fashion, status, and performance all rolled into one.
For brands, manufacturers, and importers, however, the pressure to get it right is immense. A single misstep—a loose stitch, a weak material—can jeopardize years of hard work and damage a brand’s reputation. Consequently, it may lead to costly recalls, frustrated customers, and long-term harm to the brand image.
In this guide, we’ll walk you through everything you need to know about sneaker quality control (QC). From common defects to the key inspection steps, we’ve got you covered to ensure your sneaker brand stands up to both performance expectations and customer satisfaction.
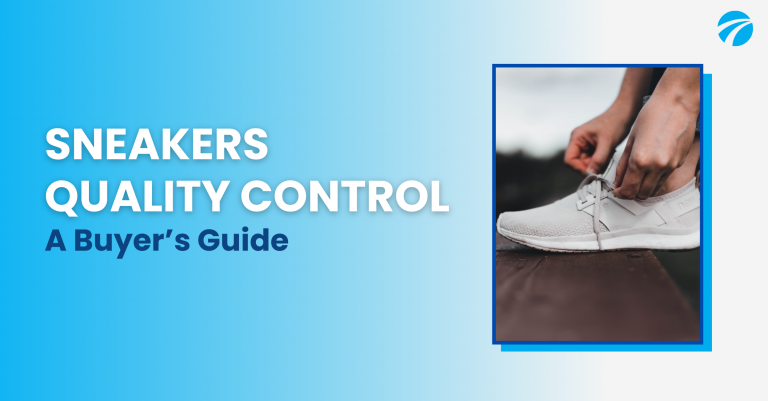
What is Sneakers Quality Control?
Sneakers Quality Control (QC) is the process of ensuring that every pair of sneakers meets the required standards of design, performance, and safety before reaching consumers. It involves a series of checks and tests conducted throughout the production process, starting with the selection of materials and continuing through to the final product.
The goal of footwear Inspection is to catch any defects early on, such as weak stitching, poor material quality, sizing inconsistencies, or bonding failures between the sole and upper. It also ensures that the sneakers perform as expected, providing comfort, support, and durability for the intended activities, whether it’s running, basketball, or casual wear.
Common Quality Defects Found During Sneaker Quality Control
When it comes to sneaker production, quality control is crucial to identifying defects that could affect the final product’s performance and durability. Here are some of the most common quality defects that inspectors often find during sneaker quality control:
Weak Bonding: One of the most common issues is glue failure between the sole and upper part of the shoe. This weak bonding can lead to premature separation, affecting both the durability and the overall look of the sneaker.
Material Defects: From inconsistent stitching to poor-quality leather or mesh, material defects can severely impact the shoe’s integrity. These flaws can lead to discomfort, reduced lifespan, and poor aesthetic appeal.
Asymmetry: Mismatched pairs are a frequent problem in sneaker production. Inspectors often find uneven stitching, different cuts, or mismatched designs between the left and right shoe, affecting both comfort and visual appeal.
Sizing Inconsistencies: Another issue that frequently arises is sizing discrepancies, where sneakers within the same batch or across different pairs may vary in size. This inconsistency can result in a poor fit, leading to customer dissatisfaction.
Foreign Objects: Occasionally, small debris or contaminants are left inside the shoe during production. These foreign objects can cause discomfort and, in some cases, pose safety risks if not identified and removed during the QC process.
Identifying these defects early in the production process helps manufacturers address issues before the shoes reach consumers, ensuring a higher quality product and reducing the risk of costly returns or damage to the brand’s reputation.
Key Elements Of Sneakers Inspection: The Tetra Inspection Approach
At Tetra Inspection, we take a multi-layered approach to shoe quality control, ensuring every detail is meticulously examined. Here’s how we break it down:
- Visual Inspection: Our trained inspectors possess a keen eye for detail. They scrutinize stitching for consistency and strength, check for asymmetry between left and right shoes, and identify any imperfections in materials or finishing touches.
- Dimension Check: We utilize specialized measuring tools to verify that every shoe adheres to the exact size specifications. This ensures a consistent fit across all pairs within a production run.
- Durability Check: We don’t just rely on visuals. We employ a battery of durability tests that simulate real-world wear and tear. This can involve flexing machines to assess material fatigue, abrasion testers to evaluate scuff resistance, and even environmental chambers to gauge how the shoe performs in extreme temperatures.
- Performance Check: For performance-oriented sneakers, we go beyond basic construction. We have specialized equipment to test features specific to the shoe’s type. Grip testers measure traction for running shoes, while impact absorption testers analyze shock mitigation in basketball footwear.
- Material inspection: We understand that the quality of materials directly impacts a sneaker’s performance and longevity. We partner with labs for in-depth material analysis, assessing aspects like strength, breathability, and moisture-wicking capabilities. This ensures the materials chosen live up to the intended function of the shoe.
Key Types of Sneakers We Inspect
Not all sneakers are created equal. Our QC experts are trained to handle a wide variety of footwear, including but not limited to:
- Athletic Shoes: Running shoes, basketball sneakers, and training footwear require rigorous testing for durability, support, and traction.
- Casual Sneakers: Everyday sneakers undergo inspections for material quality, stitching integrity, and overall comfort.
- Luxury Sneakers: High-end sneakers demand meticulous attention to detail, with inspections focusing on premium materials, flawless construction, and brand consistency.
The Sneakers Quality Control Process
The journey from raw materials to the sneakers on your feet is a detailed and intricate process that demands strict attention to quality.
At Tetra Inspection, we take pride in ensuring that every pair of sneakers passes through a comprehensive and rigorous quality control (QC) process. This guarantees that the final product lives up to the highest standards of both performance and aesthetic appeal.
Here’s how the QC process breaks down step by step:
Pre-Production Inspection for Sneakers
The QC process begins before production even starts. Our inspectors scrutinize the raw materials—whether it’s fabric, synthetic leather, adhesives, or rubber soles—to make sure they meet the quality requirements. The goal here is to prevent any issues from arising later in production. We don’t just rely on visual checks. Each material sample is tested in specialized labs for factors like strength, breathability, and chemical compliance. This proactive testing ensures that only the highest quality materials make their way into the production line, reducing the risk of defects in the final product.
During Production Inspection for Sneakers
As the sneakers are being assembled, quality control doesn’t stop—it intensifies. Inspectors are stationed at key points in the production process to monitor the quality at every stage. For example, stitching is closely inspected to ensure that every seam is secure and neat. Any inconsistencies in stitching can weaken the structure of the shoe or lead to discomfort for the wearer.
Inspectors also verify that the sole is properly bonded to the upper, ensuring that there are no adhesion issues that could cause the shoes to fall apart.
Furthermore, each shoe’s sizing and labeling are double-checked to ensure that they match the specifications, preventing any errors in distribution.
Pre-Shipment Inspection for Sneakers
Before any sneakers leave the factory, they undergo a final, meticulous review. This step involves inspecting the finished product from every angle. Inspectors will assess the overall aesthetics, checking for imperfections such as scuffs, uneven coloring, or loose threads. The symmetry between the left and right shoes is also checked carefully to ensure that they are identical in shape and size. Moreover, inspectors confirm that the final dimensions of the shoes match the sizing specifications exactly. This ensures that no product leaves the facility without meeting the necessary standards.
Additional Testing
Depending on the type of sneaker, specialized performance tests are carried out to verify that each pair functions as intended.
For example:
-
Grip and Traction Testing for Running Shoes: Running shoes need excellent grip to avoid slipping, particularly on wet or uneven surfaces. We use testing methods to simulate real-world conditions and ensure that the sole provides enough traction to keep runners safe and stable.
-
Impact Absorption Testing for Basketball Shoes: For basketball shoes, the ability to absorb shock is critical. Our testing measures how well the shoe cushions the foot with each jump, ensuring that players’ knees and joints are protected.
-
Flexibility and Support Testing for Training Shoes: Training shoes require a balance of flexibility and support to handle a variety of movements. We test the shoe’s flexibility in key areas to ensure it provides enough support during exercises like squats or lateral movements.
These additional tests ensure that each sneaker performs as expected, offering the right mix of comfort, support, and durability for its intended activity.
Documentation and Reporting
We believe that transparency is key to maintaining high-quality standards, which is why every step of the QC process is thoroughly documented. This includes detailed inspection reports that outline the process and highlight any defects that were identified. Photographs are taken of any issues, and corrective action plans are drafted to address them before mass production continues. This documentation creates a reliable audit trail, which helps manufacturers track trends in quality issues and implement continuous improvements in their processes.
Through this rigorous QC process, we ensure that each pair of sneakers meets both performance and aesthetic expectations. From the very first inspection of raw materials to the final pre-shipment check, we are committed to delivering products that not only look good but also perform at their best—safeguarding your brand’s reputation and ensuring customer satisfaction.
Sneaker and Footwear Quality Standards in the US and Europe
While the US and Europe prioritize safety in footwear, their approach differs slightly:
Mandatory Standards:
US: The Consumer Product Safety Improvement Act (CPSIA) restricts harmful chemicals in footwear. Additionally, specific footwear types like work boots might need to comply with American Society for Testing and Materials (ASTM) standards like F2412 for protective features.
Europe: The General Product Safety Directive (GPSD) ensures all footwear sold in the EU is safe. Manufacturers can achieve compliance by following harmonized standards like EN ISO 20345 for safety footwear. This standard focuses on aspects like slip resistance and impact protection. Additionally, the EU mandates labeling footwear materials under Directive 94/11/EC.
How Tetra Inspection Can Help
With a network of over 500 inspectors across 40 countries, Tetra Inspection provides comprehensive inspections throughout the production process. Our in-depth footwear industry expertise allows us to identify and prevent potential quality issues. In addition, we stay on top of international regulations to guarantee your sneakers meet all safety and quality standards in different markets.
To learn more about our Sneakers Quality Control services, get in touch with us today!