Bringing a new baby into the world is a time filled with joy and meticulous preparation. As parents carefully select every item to ensure their little one’s safety and comfort, manufacturers bear the crucial responsibility of meeting stringent quality standards. In the United States, the regulatory landscape for baby products is both comprehensive and unforgiving, reflecting the high stakes involved in safeguarding our youngest consumers.
In this guide, we’ll unpack the essential regulations, explore specific product requirements, and provide actionable insights to help you ensure your baby products meet the highest safety benchmarks.
The Importance of Regulatory Compliance
Beyond a legal requirement, regulatory compliance for baby products in the United States plays a vital role in protecting the well-being of children. The regulations set forth by governing bodies such as the Consumer Product Safety Commission (CPSC), Food and Drug Administration (FDA), and ASTM International are designed to identify and mitigate risks at every stage of a product’s lifecycle—from design and manufacturing to distribution and use.
Compliance with these standards has a dual benefit. For consumers, it ensures that baby products meet safety benchmarks, reducing the likelihood of injuries or fatalities. For businesses, compliance is a strategic imperative. Adhering to these standards minimizes the risks of recalls, lawsuits, and reputational damage, all of which can have devastating financial and operational consequences. Moreover, it demonstrates a company’s commitment to safety and reliability, building trust with parents and caregivers who demand the highest levels of quality for their children.
Key Regulations and Standards
Consumer Product Safety Improvement Act (CPSIA)
The CPSIA is a cornerstone of U.S. children’s product safety regulations. It mandates third-party testing and certification for all children’s products, ensuring that they meet stringent safety criteria before entering the market. This requirement is non-negotiable and covers a broad spectrum of safety concerns, including lead content, phthalate restrictions, and mechanical safety. The act also includes requirements for clear, accessible labeling, ensuring that consumers are informed about proper product use and potential hazards.
Â
For manufacturers and importers, CPSIA compliance involves investing in accredited testing facilities and maintaining meticulous records of certifications. The act also places significant emphasis on traceability, requiring businesses to include tracking labels on products to identify the manufacturing date and location. This traceability is crucial for managing recalls and addressing potential safety issues promptly.
Â
ASTM International Standards
ASTM International provides voluntary performance and safety standards for a wide range of baby products, including strollers, cribs, and toys. These standards are developed collaboratively by industry experts, regulators, and consumer representatives, making them comprehensive and practical.
Â
While ASTM standards are technically voluntary, they often become de facto requirements due to their adoption by regulatory bodies like the CPSC. For example, ASTM F833 outlines rigorous safety specifications for strollers, addressing stability, durability, and mechanical integrity. Similarly, ASTM F963 is the gold standard for toy safety, covering hazards like choking, toxic substances, and flammability. Manufacturers that align with ASTM standards benefit from a structured framework for risk mitigation, enhancing product reliability and consumer confidence.
Â
FDA Guidelines
The FDA’s role in regulating baby products primarily concerns food-contact items, such as bottles, pacifiers, and feeding utensils. These guidelines are rooted in scientific research and focus on eliminating harmful chemical exposures. For instance, the FDA has banned the use of BPA (bisphenol A) in baby bottles and sippy cups due to its potential health risks.
Â
Manufacturers must conduct rigorous migration testing to ensure that materials used in food-contact products do not leach harmful substances. Compliance with FDA guidelines is not only a legal requirement but also a critical factor in reassuring parents about the safety of feeding products.
Â
16 CFR Regulations
The Code of Federal Regulations (CFR) under Title 16 encompasses federal rules that address a range of safety concerns for baby products. Key areas include:
Â
- Hazardous Substances: Restrictions on toxic chemicals, such as lead and phthalates, to protect children from long-term health risks.
- Flammability Standards: Requirements for materials to resist ignition, reducing the risk of fire-related injuries.
- Mechanical Safety: Specifications to prevent choking, entanglement, and sharp-edge hazards.
The enforcement of 16 CFR regulations is robust, with the CPSC conducting routine inspections and penalizing non-compliance. For businesses, aligning with these rules involves proactive design, material selection, and quality assurance processes to eliminate potential hazards.
Compliance and Standards for Specific Baby Products in the US
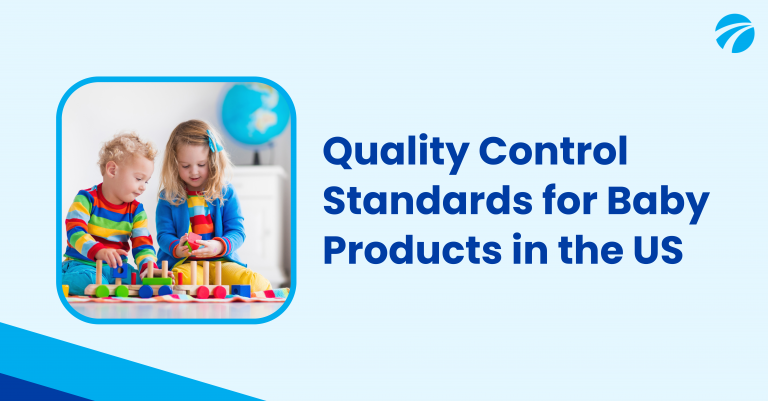
Â
Cribs and Sleeping Products
Cribs, bassinets, and other sleeping products are among the most highly regulated baby products due to the critical safety risks they pose, including entrapment, suffocation, and structural failure. Federal regulations, such as 16 CFR Part 1219 for full-size cribs and 16 CFR Part 1220 for non-full-size cribs, establish mandatory requirements to ensure these products provide a safe sleeping environment.
Â
Key Requirements:
- Slat Spacing: The spacing between crib slats must not exceed 2 3/8 inches. This is to ensure that an infant’s head or limbs cannot become trapped, which could result in serious injury or death.
- Mattress Fit: A snug fit between the mattress and the crib frame is mandatory, with no more than a two-finger gap allowed. This prevents the risk of suffocation caused by a baby becoming wedged between the mattress and crib.
- Structural Integrity: Cribs must endure durability tests that simulate prolonged and repeated use. They must not loosen, collapse, or exhibit signs of structural compromise.
Inclined sleepers, which have been subject to significant regulatory scrutiny, must comply with ASTM F3118. These standards address specific risks related to inclined angles and stability, ensuring the product minimizes suffocation hazards while maintaining structural integrity during use.
Â
Strollers and Carriages
Strollers and carriages are everyday essentials for parents, and their safety and usability are critical. The ASTM F833 standard outlines safety specifications for these products, focusing on mechanical durability, stability, and proper functioning under stress. Given the high frequency of use and varying terrains they encounter, robust testing is essential to identify potential hazards.
Â
Key Requirements:
- Effective Brakes: Parking brakes are tested to confirm they remain engaged even when subjected to significant force. This is particularly crucial on inclined surfaces where rolling could lead to severe accidents.
- Stability: Products must pass tipping tests, ensuring they remain upright even when weight is distributed unevenly or when accessories, such as diaper bags, are attached.
- Durability: Folding mechanisms and other components are subjected to repetitive use simulations to confirm that they do not wear out or fail prematurely. This prevents hazards like sudden collapse during use.
- Entrapment Prevention: Design features are analyzed to eliminate spaces where a child’s fingers, limbs, or clothing could become trapped. This includes testing all moving parts and adjustable features.
Clear instructions and warnings are legally required to educate parents about proper usage, assembly, and maintenance. Misuse is often a result of unclear labeling, which can lead to avoidable injuries.
Â
Toys and Small Parts
Toys for young children, particularly those under three years old, are subject to stringent safety regulations outlined in ASTM F963 and the Federal Hazardous Substances Act (FHSA). These standards aim to mitigate risks such as choking, exposure to toxic chemicals, and fire hazards.
Â
Key Requirements:
- Small Parts Hazard: Toys intended for infants and toddlers must not include detachable parts that fit inside a small parts cylinder. This testing simulates the dimensions of a child’s airway to prevent choking incidents.
- Lead and Toxic Substances: Materials must contain no more than 100 ppm of lead and comply with strict limits on phthalates and other harmful chemicals. These restrictions reduce risks of developmental harm from prolonged exposure.
- Flammability Resistance: Toys must be made from materials that resist ignition and slow the spread of fire. This is particularly important for plush toys and those used near heat sources.
These comprehensive requirements ensure toys are safe for daily use, reducing preventable injuries and providing peace of mind to parents.
Â
Feeding Products
Baby bottles, pacifiers, and other feeding products are regulated under FDA guidelines due to their direct contact with food and liquids. These products not only require physical safety but also must be free from chemical hazards that could leach into food during use.
Â
Key Requirements:
- Material Safety: BPA and other harmful chemicals are banned in materials used for feeding products. These products are tested for chemical leaching, especially when exposed to heat, ensuring they meet FDA safety thresholds.
- Sterility and Hygiene: Manufacturing processes must adhere to strict sterility standards to prevent bacterial contamination. Testing ensures that no harmful microbes are present during the product’s lifecycle.
- Migration Testing: Products are subjected to heat and chemical exposure tests to ensure no harmful substances migrate into liquids or foods during use.
These standards ensure that feeding accessories not only last but also remain safe under everyday conditions, such as frequent washing and sterilization.
Â
High Chairs and Booster Seats
High chairs and booster seats are regulated under ASTM F404, which sets detailed safety requirements for stability, structural integrity, and secure restraint systems. These products must support active infants and toddlers without tipping or collapsing, even under uneven weight distribution or vigorous movement.
Â
Key Requirements:
- Stability Testing: High chairs must remain upright when subjected to weight shifts or external forces. This ensures that a child’s natural movements will not cause tipping, which could result in injuries.
- Durability of Restraint Systems: Straps and buckles are tested to withstand repeated use and must not wear out or break over time. Restraint systems are critical in keeping children secure, especially during mealtime activities.
- Assembly and Usage Instructions: Clear, concise instructions are required to help parents correctly assemble and use the product. Misuse due to unclear directions can lead to accidents that proper education could prevent.
Manufacturers must invest in robust testing to identify potential weak points in design and provide products that perform reliably throughout their intended use period.
Â
Chemical Safety in Baby Products
Chemical safety is a cornerstone of quality control in baby products, reflecting both regulatory mandates and public health concerns. Children are uniquely vulnerable to chemical exposure due to their smaller body sizes, developing systems, and behaviors such as mouthing objects. To address these risks, U.S. regulations strictly limit harmful substances in baby products, requiring manufacturers to adhere to rigorous standards.
Â
Lead and Heavy Metals
Lead exposure in children can cause severe developmental and neurological issues, even at low levels. To mitigate this risk, the U.S. enforces strict limits under 16 CFR 1303, which caps lead content in surface coatings at 100 ppm. This regulation extends to paints, finishes, and any other accessible parts of a baby product. Manufacturers must conduct regular lead testing throughout production to ensure compliance, especially when sourcing materials from regions with varying regulatory practices. Failure to meet these standards can result in severe penalties, recalls, and reputational damage.
Â
Phthalates
Phthalates are plasticizers commonly used to make materials flexible. However, research has linked these chemicals to hormonal disruptions and developmental issues in children. The Consumer Product Safety Improvement Act (CPSIA) restricts six specific phthalates, including DEHP and DBP, to a concentration of 0.1% in any accessible part of children’s products. This limit is particularly important for items such as teething rings, pacifiers, and soft plastic toys, as these are often mouthed by infants.
Â
Manufacturers must implement robust testing protocols to measure phthalate concentrations in raw materials and finished goods. Third-party laboratories accredited by the CPSC are essential for accurate testing, as phthalates can sometimes migrate from packaging or adjacent materials during storage.
Â
Flame Retardants
Flame retardants are chemicals used to reduce the flammability of materials, particularly in textiles and foam. While these substances can lower fire-related risks, certain flame retardants, such as PBDEs, have been linked to cognitive and behavioral issues in children. Many U.S. states, including California, have implemented additional restrictions on specific flame retardants in baby products.
Â
Manufacturers are encouraged to use non-toxic alternatives or explore inherently flame-resistant materials to meet these standards. For instance, instead of chemically treated foams, textiles with natural fire-resistant properties, such as wool, are gaining traction as safer substitutes. Comprehensive testing is necessary to confirm that these alternatives meet both safety and performance expectations.
Â
Baby Products Quality Control and Certification Requirements in the US
Testing and certification are vital steps in ensuring that baby products meet stringent U.S. safety standards. These processes are designed to identify and eliminate potential hazards, verify compliance with regulations, and provide peace of mind to both manufacturers and consumers. Every stage, from product development to final production, must undergo thorough evaluation.
Â
Testing and Certification Requirements
To sell baby products in the U.S., manufacturers must conduct testing at CPSC-accredited laboratories. These facilities are equipped to perform comprehensive assessments, ensuring that products meet safety, durability, and chemical standards. Accredited labs follow standardized procedures that ensure the reliability and reproducibility of results, giving manufacturers confidence in their product safety claims.
Key Phases in the Testing Process
Prototype Testing: The first step in testing involves evaluating product prototypes. During this phase, engineers and safety experts analyze the design to identify potential hazards such as sharp edges, entrapment risks, or structural weaknesses. For example, cribs are tested to ensure that slat spacing prevents head entrapment and that the structure remains stable under repeated stress.
Â
Batch Testing: Batch testing is conducted during production to ensure consistency in quality and safety across all units. This step is critical in catching manufacturing defects or material inconsistencies that might have been missed during the prototype phase. Regular batch testing helps maintain compliance and minimizes the risk of recalls.
Â
Label Verification: Clear and accurate labeling is not just a regulatory requirement but also a vital part of consumer safety. Labels must include warnings, usage instructions, and safety guidelines that are easy to understand. Testing ensures that these labels remain legible and durable, even under conditions such as heat, moisture, or frequent handling.
Â
Children’s Product Certificate (CPC): The CPC is a legally required document that certifies a product’s compliance with all applicable U.S. safety standards. This certification must be based on testing performed by a CPSC-accredited lab. The CPC provides detailed information about the product, including the manufacturing date, batch number, and the specific standards met, offering transparency and accountability.
How Tetra Inspection Can Help Ensure Quality and Compliance
With operations in over 40 countries and a team of 500 highly experienced quality control inspectors, Tetra Inspection ensures your baby products meet the highest safety and compliance standards. We specialize in U.S. regulatory requirements, from CPSIA to ASTM, and provide services such as product inspections, factory audits, and lab testing through accredited U.S. laboratories.Â
Â
By identifying potential risks and ensuring compliance at every stage, we help you avoid costly recalls and build consumer trust. Our tailored solutions are designed to meet the unique challenges of your product line.Â
Â
Contact Tetra Inspection today to ensure your products are safe, compliant, and market-ready.
Â