Ensuring top-notch quality isn’t just about having great products or services. It’s about having a robust Quality Management System (QMS) in place – and QMS audits are the backbone of ensuring that your system is up to par.
Let’s dive into everything you need to know about QMS audits.
Ensuring a top-notch Quality Management System (QMS) is essential for any business committed to maintaining high standards and consistent quality. A QMS audit plays a pivotal role in assessing the effectiveness of your system, helping identify areas for improvement, and ensuring compliance with industry standards like ISO 9001. In this guide, we’ll explore everything you need to know about QMS audits, including the different types, their importance, and how to prepare for a smooth and successful audit process. Whether you’re new to audits or aiming to refine your approach, this article provides valuable insights for your QMS journey.
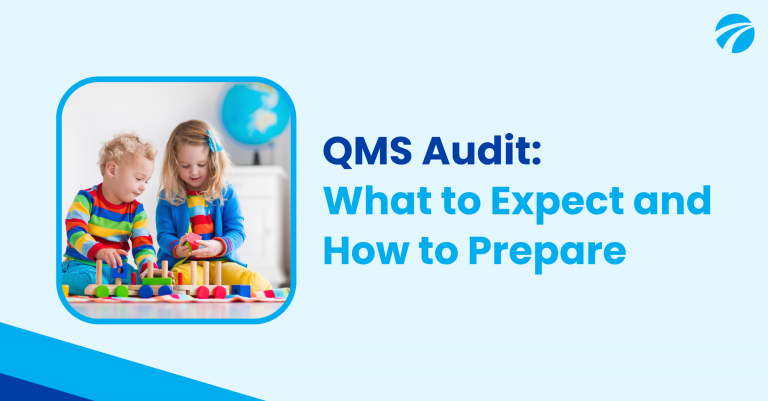
Difference Between Quality Audit vs. QMS Audit
What is a Quality Audit?
Let’s begin by clarifying the difference between a quality audit and a QMS audit. A quality audit is a broader concept, encompassing any systematic examination of a process or system to determine its effectiveness in meeting predefined requirements. This could involve auditing a specific production line, or a supplier’s quality control practices.
What is a QMS Audit?
A QMS audit, on the other hand, has a more specific focus. It’s a comprehensive evaluation of a company’s entire Quality Management System. This audit assesses how well the QMS aligns with relevant standards (like ISO 9001) and its own documented procedures. It essentially verifies if the system is designed and implemented effectively to achieve consistent quality output.
Types of QMS Audits
QMS audits aren’t one-size-fits-all, and the type you’ll need depends on your goals.
Let’s break down the key categories:
- Internal Audits: Think of these as a self-examination. You train your own employees to be auditors, and they systematically assess your QMS. Internal audits are fantastic for maintaining a culture of continuous improvement. They help you find and fix problems before they become major issues. However, they can’t replace external audits when it comes to demonstrating compliance to customers or obtaining certifications.
- Second-Party Audits: These audits are conducted by your customers or other interested stakeholders. For example, a large company might audit its key suppliers to ensure that their quality systems will produce parts that meet the company’s exacting standards. Second-party audits can be a valuable way to strengthen business relationships and build trust in your quality processes.
- Third-Party Audits: For the highest level of independence and objectivity, you have third-party audits. These are performed by external certification bodies who specialize in auditing against specific standards (like ISO 9001). Passing a third-party audit often results in official certification, which can be a major marketing advantage and signal of quality to customers.
Why Conduct a QMS Audit?
QMS audits might seem like additional work at first glance, but they offer significant benefits that make them well worth the effort. Here’s why they are so important:
Â
- Compliance: In many industries, QMS audits aren’t just a good idea; they’re a requirement. Regulations or internationally recognized standards (like ISO 9001) often mandate regular audits. Failing to comply can lead to fines, loss of business, or even being forced to shut down.
- Continuous Improvement:Â A QMS audit digs deep, revealing the true health of your quality system. It’s one thing to have impressive procedures written down; it’s another to see them working in practice. Audits pinpoint strengths, but more importantly, they uncover those hidden inefficiencies or gaps in processes that might be silently affecting your product or service quality. This awareness gives you the roadmap to get even better.
- Risk Management: It’s a lot cheaper to fix a problem during an internal audit than to deal with the fallout of a product recall or a dissatisfied major customer. Audits force you to carefully examine your processes, helping you spot potential quality issues before they snowball into a full-blown crisis.
- Customer Confidence: Quality is Your Selling Point.Customers want more than just products. Demonstrating your commitment to quality through regular audits builds trust and sets you apart from competitors. Certifications from respected third-party auditors can be a powerful marketing tool, attracting new customers and opening up opportunities.
Conducting a QMS Audit According to ISO 9001
ISO 9001 is the most widely used quality management standard globally. If your goal is achieving ISO certification or maintaining compliance, you need to understand how to perform audits that align with this standard. Here’s a walkthrough of the key phases involved:
Â
Planning is Everything: Start with a solid foundation. Clearly define the scope of the audit, which parts of your QMS (or even specific locations) will be assessed. Assemble your audit team, selecting individuals with the necessary skills and knowledge of ISO 9001. Develop a detailed audit schedule that allows sufficient time for each stage of the process.
Â
Gathering Evidence: This is where the rubber hits the road. Auditors employ various techniques to assess the effectiveness of your QMS. They’ll dig deep into your documentation, reviewing policies, procedures, and records. They’ll interview staff members at all levels to understand how processes work in practice. Additionally, auditors may observe processes in action to see if what’s happening matches what your procedures describe.
Â
Analysis and Insight: Don’t just list discrepancies; seek to understand why they occurred. Compare your findings against the specific requirements laid out in the ISO 9001 standard. Seek to identify the root causes of non-conformances, as this will guide the development of effective corrective actions.
Â
The Audit Report: A well-written audit report documents findings clearly and factually. It separates non-conformances from more minor observations and provides specific recommendations for improvement. This report becomes the roadmap for taking the necessary steps to strengthen your QMS.
Â
Corrective Actions: The audit isn’t over until you’ve addressed the root causes of issues found. This requires implementing corrective actions that are designed to not only fix the immediate problem but also prevent it from recurring. Follow-up may be needed to ensure the effectiveness of these actions.
Â
Common QMS Audit Findings
While the specific issues uncovered in a QMS audit will vary from company to company, there are recurring themes that auditors often encounter. Being aware of these common pitfalls can help you proactively address them within your organization. Here’s a look at some of the most frequent findings:
Â
- Documentation Control: Issues with document control are widespread. These might include outdated procedures, missing or incomplete records, or a lack of clarity in how quality-related documents are managed.
- Management Commitment: A successful QMS depends on strong leadership. Quality Auditors look for evidence that management not only talks the quality talk but also allocates resources, sets clear quality objectives, and remains actively involved in reviewing quality performance.
- Inadequate Training: Even great procedures are useless if employees aren’t properly trained in following them. Auditors will assess whether your staff has the necessary knowledge and skills to do their jobs in a way that consistently meets quality standards.
- Poor Process Control: Are your core processes for producing goods or delivering services well-defined, monitored, and consistently executed? Auditors will be searching for gaps in quality control and variability that could lead to defects or inconsistent outcomes.
- Corrective Action Shortcomings: It’s not enough to just find a problem; you need to fix it and address the root cause to prevent it from happening again. Auditors focus on whether your corrective action system is robust and effective in driving lasting improvements.
- Customer Feedback Loop: Do you have a system for collecting, analyzing, and acting on customer feedback? This includes everything from complaints to surveys. Auditors want to see that you’re using customer insights to improve your products, services, and the overall customer experience.
Preparing for a Smooth QMS Audit
Undergoing a QMS audit doesn’t need to be a stressful experience. Here are some valuable tips to ensure a smooth and successful audit:
Â
- Conduct Mock Audits: Perform internal mock audits to identify areas for improvement before the official audit. This helps your team become familiar with the audit process and address potential weaknesses.
Â
- Ensure Documentation Readiness: Review and update all QMS documentation to ensure its accuracy and completeness. Have all relevant records readily available for the auditors to examine.
Â
- Train Employees on QMS and Audit Expectations: Educate your employees about the QMS, their respective roles within the system, and what to expect during the audit process. This will help them feel confident and prepared to answer audit questions.
How Tetra Inspection Can help with QMS Audit
Tetra Inspection offers specialized QMS audit services for businesses of all sizes. Our experienced auditors help you identify areas for improvement, ensure compliance with industry standards like ISO 9001, and streamline your quality processes. Â
With Tetra Inspection, you can achieve a robust quality management system that drives customer satisfaction and overall business success. Â
Â
Contact us today to schedule a consultation and see how we can support your quality goals.