Initial Production Check
Initial Production Check: Ensuring Quality And Efficiency In Supply Chains
Looking to ensure quality and efficiency in your supply chain? Our Initial Initial Production Check (IPC) services can help you achieve just that. With our highly qualified inspectors, you can trust that your products will meet your specifications and comply with international standards.
What Is Initial Production Check And Why Is It Important?
The IPC process typically involves the following steps:
- Review of raw materials and components to ensure they meet the required standards.
- Inspection of production equipment and machinery to verify proper operation and maintenance.
- Assessment of production processes to identify any areas of concern or potential.
- Evaluate the initial product samples to confirm they meet the agreed-upon quality specifications.
Why is Initial Production Check Important?
Initial Production Check offers many benefits that ultimately translate into higher customer satisfaction and increased profitability. Here are some of the reasons
why Initial Production Inspection is important:
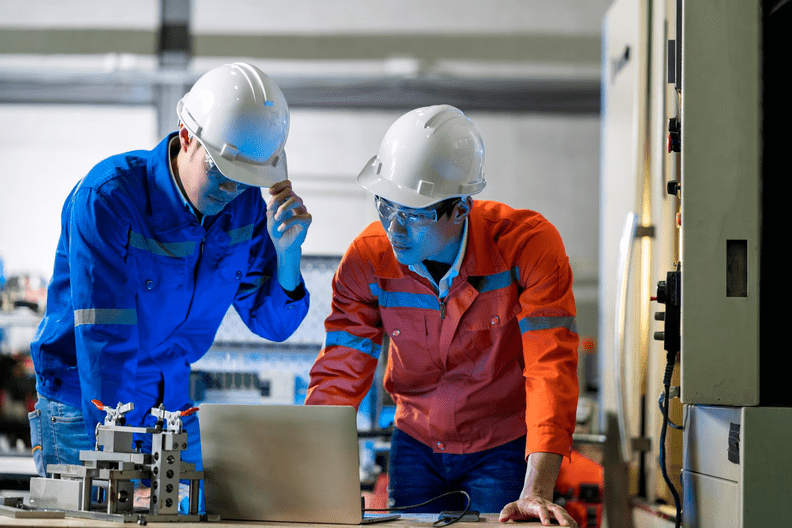
Benefits Of Initial Production Check
Initial Production Check (IPC) is a vital tool that enables businesses to achieve excellence by offering a comprehensive understanding of their production process. In addition to the benefits previously discussed, IPI has numerous advantages that highlight its value in modern business operations.
Initial Production Inspection Process Explained: What To Expect
Tetra Inspection plays a vital role in the Initial Production Inspection process by providing expert inspectors with extensive experience and a deep understanding of industry standards. Tetra Inspection follows a stringent inspection protocol, ensuring consistency and accuracy in its findings.
As an independent third-party inspection company, Tetra Inspection is a neutral party, providing unbiased assessments and valuable insights. We work with our clients to meet their unique requirements and tailor the inspection process accordingly.
A GUIDE FOR BRANDS AND IMPORTERS
When To Schedule An Initial Production Check
- Production Lead Time Understanding the production lead time is vital for scheduling an IPI effectively. Production lead time is when an order is placed to when the finished goods are ready for shipment. An IPI should take place after the production line has been set up and a small portion of the order is completed. This provides an opportunity to identify and rectify potential issues before they escalate.
- Seasonality and Industry Dynamics Considering the seasonality and industry dynamics can impact the optimal timing for an IPI. For instance, suppliers might be overwhelmed with orders during peak seasons, leading to potential quality issues. Conducting an IPI early in production can help address these challenges and maintain quality standards..
- Complexity of the Product The complexity of the product plays a significant role in determining the ideal time for an IPI. Complex products with intricate designs or advanced technology may require additional time for inspection. In such cases, scheduling the IPI earlier in the production process is wise to allow for adjustments and improvements.
- Supplier’s Track Record It is wise to schedule an Initial Production Inspection (IPI) early in the production process if you are working with a new supplier or a supplier that has a track record of quality issues. This can help you ensure that your specific requirements are being met. On the other hand, with a trusted supplier who consistently delivers high-quality products, you may choose to schedule the IPI later in the production process.
- Regulatory and Compliance Requirements Finally, consider any regulatory and compliance requirements relevant to your industry. These standards may necessitate more frequent inspections or require inspections at specific stages of production. Factor in these requirements when planning the timing of your IPI.
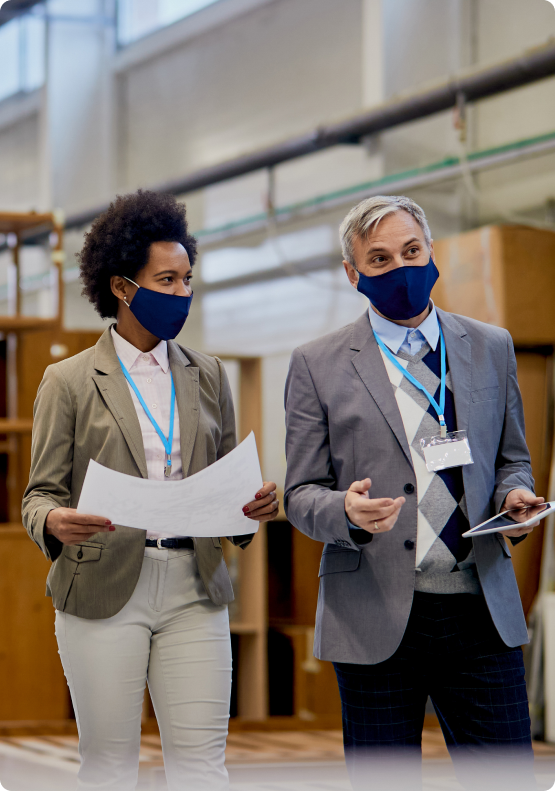
Initial Product Checking
During Production Inspection
20-40% Production Complete
Performed when around 20-80% of the production is complete to identify issues early on and monitor production progress.
Pre-Shipment Inspection
80-100% Production Complete
Scheduled when 80-100% of the production is completed and at least 80% of the products are packed,
Container Loading Check
100% Production Complete
Comprehensive Checklist
What Checks Are Carried Out During An Initial Production Inspection?
Factory Compliance
- Assess the factory’s certifications and licenses.
- Evaluate the factory’s health, safety, and environmental practices.
- Review labour conditions and compliance with local laws.
Production Plan Verification
- Confirm the production schedule and deadlines.
- Ensure the availability of raw materials and components.
- Check machinery and equipment for efficiency and safety.
Product Specifications Review
- Verify product designs, dimensions, and materials.
- Ensure the correct colour, texture, and finish.
- Check labelling, packaging, and shipping requirements.
Quality Control Procedures
- Review the factory’s quality control plan.
- Confirm inspection and testing methods.
- Assess the factory’s quality management system (QMS).
Quality Control Procedures
- Review the factory’s quality control plan.
- Confirm inspection and testing methods.
- Assess the factory’s quality management system (QMS).
Pre-Production Samples
- Inspect pre-production samples for design and quality.
- Compare samples with approved prototypes.
- Confirm the product’s conformance to standards and specifications.
Raw Materials and Components Inspection
- Check the quality and specifications of raw materials.
- Verify the supplier’s certifications and documentation.
- Inspect components for defects and inconsistencies.
Production Monitoring
- Regularly assess production progress.
- Review production reports and records.
- Communicate with factory management to address any concerns.
Trust Tetra Inspection
Why Choose Tetra Inspection For Initial Production Inspection
Expertise And Experience
Customized Services
Comprehensive Inspection Reporting
Fast Turnaround Time
Schedule Your Furniture Inspection Today
shipment, minimizing risks and ensuring compliance with international standards.
Common Questions About
Initial Production Inspection
The cost of a pre-shipment inspection depends on the pricing plan you choose. Here are the available options:
Â
Standard Rate:
- Price: $240 per man-day
Monthly Plan
- Price: $189 per man-day (over 20% savings)
- Billed Monthly at $1,899 for 10 inspections across Asia
Annual Plan (Recommended):
- Price: $158 per man-day (over 35% savings)
- Billed Monthly at $1,584 for 120 inspections across Asia (12 months subscription)
- Â
BLOG
Related Articles
shipment, minimizing risks and ensuring compliance with international standards.