Factory Audit
Meeting ISO 9001 Standards For Quality And Compliance
Factory Audit
Factory Audit: Meeting ISO 9001 Standards For Quality And Compliance
Is your factory struggling to meet the rigorous requirements of ISO 9001 Standards for quality and compliance? Don’t let subpar processes and inadequate systems hinder your production efficiency and product excellence. Tetra Inspection is here to help. Our highly experienced factory auditors will thoroughly assess your manufacturing facility, evaluating your processes, quality management systems, and compliance with ISO 9001 Standards. Schedule your Factory Audit today and take the first step towards manufacturing excellence.
FACTORY AUDIT
What Is A Factory Audit
A factory audit is an in-depth evaluation of a manufacturing facility’s adherence to industry
standards
, regulatory requirements, and contractual obligations. It aims to ensure consistent product quality, a safe working environment, and ethical practices. The audit includes examining the facility’s quality management system (QMS), such as ISO 9001 certification, highlighting a commitment to quality, customer satisfaction, and continual improvement.
Factory Audit Based on ISO 9001:
ISO 9001
is a widely recognized QMS standard that provides a framework for organizations to meet customer and regulatory requirements consistently. The basis of the ISO standard lies in seven quality management principles (QMP), which provide organizations with guidance to improve quality and customer satisfaction:
- Customer Focus: Organizations must understand their customers’ needs and expectations to provide products and services that meet or exceed their requirements.
- Leadership: Establishing a clear vision, mission, and values for the organization and fostering a culture of quality and continuous improvement are imperative, highlighting the significance of effective leadership.
- Engagement of People: Organizations must engage and empower their employees to contribute to quality improvement efforts and achieve their objectives.
- Process Approach: A process-based approach to quality management ensures that processes are designed and implemented to achieve the desired results and are continually monitored and improved.
- Improvement: Continual improvement is a fundamental principle of quality management, and organizations must strive to enhance their performance by identifying and addressing areas for improvement.
- Evidence-Based Decision Making:Organizations must make decisions based on objective data and evidence rather than intuition or opinion.
- Relationship Management: Organizations must establish positive relationships with suppliers, customers, and other stakeholders to achieve mutual benefits.
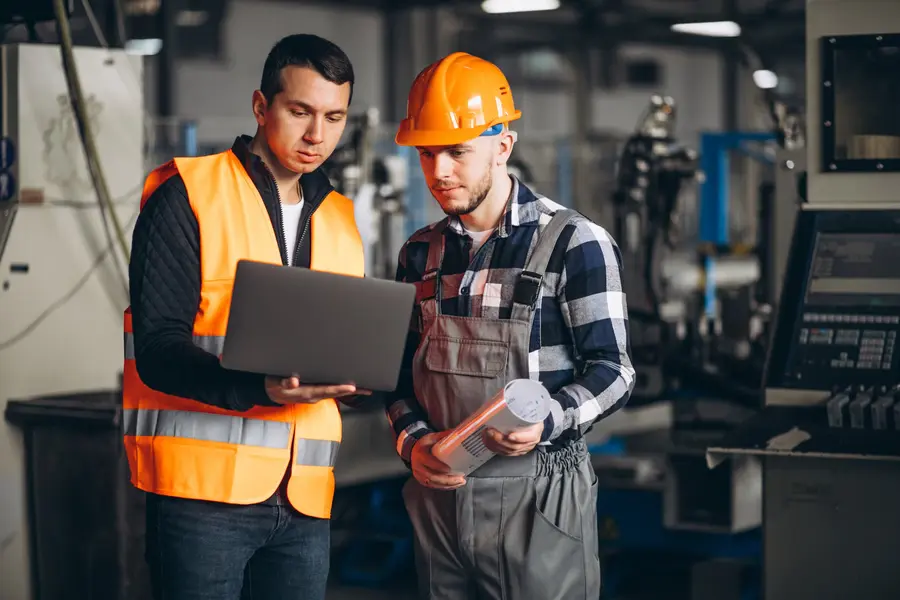
Factory Audit
Why Is A Factory Audit Important?
A factory audit is a critical tool in evaluating and validating the manufacturing capabilities, quality management systems, and overall performance of suppliers. Conducting a thorough factory acceptance test is essential in maintaining supply chain efficiency and mitigating risks associated with non-compliance and product defects.
Key benefits of factory audits:
- Quality Assurance: Aligning with internationally recognized standards, such as ISO 9001, ensures that suppliers adhere to best practices in quality management. Factory Inspection helps identify gaps in process control, product design, and customer satisfaction, enabling organizations to make informed decisions and drive continuous improvement.
- Supply Chain Transparency: Factory audits provide insights into supplier performance, revealing potential weaknesses in production, labor practices, and environmental management. This transparency enables companies to make better sourcing decisions and mitigate potential risks, fostering sustainable and ethical supply chains. .
- Compliance with Regulations: Factory audits help organizations ensure compliance with national and international regulations, including labor laws, environmental standards, and industry-specific requirements. Product compliance issues can lead to significant fines, legal consequences, and reputational damage..
- Cost Optimization: Factory audit helps identify inefficiencies and areas for improvement and can contribute to cost optimization. Implementing corrective actions can reduce waste, increase productivity, and better resource allocation, resulting in long-term cost savings.
- Strengthening Business Relationships: Factory audits facilitate open communication and mutual understanding between buyers and suppliers. Demonstrating commitment to quality and ethical practices fosters trust and promotes long-lasting business relationships, benefiting both parties.
- Does the factory have a documented quality control plan ?
- Are there any deviations from the documented system?
- Are there any corrective and preventive actions in place to address any deviations found?
During the
supplier audit
, our inspectors will review the supplier’s licenses, certifications, and permits to ensure they comply with the applicable laws and regulations
- Is there a documented maintenance program in place for all equipment?
- Are the maintenance activities being carried out as per the program?
- Are there any breakdowns or malfunctions in the equipment?
- Are there established protocols to guarantee the usage of the correct material?
- Are the raw materials being inspected upon receipt?
- Are there any deviations from the material control procedures?
The inspection team will assess the supplier’s production processes and procedures, as well as the skill levels of their employees, to ensure that they can produce products that meet the required standards.
- Are there documented training programs for all employees?
- Are the employees following the correct procedures?
- Are there any deviations from the training program?
- Are there documented training programs for all employees
- Are the employees following the correct procedures?
- Are there any deviations from the training program?
Factory Audit Services
Comprehensive Factory Audit By Tetra Inspection
Pre-Audit Review
Tetra Inspection conducts a pre-audit review of the supplier’s documentation to determine the adequacy of its quality management system
On-Site Audit
A specially trained QMS team from Tetra Inspection visits the supplier’s factory to audit the quality management system comprehensively. The audit team evaluates various critical aspects of the supplier’s operation, including customer focus, leadership, employee engagement, systematic approach to procedures, capacity for improvement, decision-making model, and relationship management.
Factory Audit Report & Certification
After completing the on-site audit, Tetra Inspection provides the vendor with a Factory Audit report, which includes a summary of the findings, recommendations for improvement, and an action plan. If the supplier meets the ISO 9001 standards, Tetra Inspection provides a certification.
Follow-Up Audit
Tetra Inspection conducts a follow-up audit to verify that the vendor has implemented the improvement recommendations and taken the necessary corrective actions.
Schedule Your Factory Audit Today
Trust our expert team of highly experienced inspectors to thoroughly inspect your products before
shipment, minimizing risks and ensuring compliance with international standards.
shipment, minimizing risks and ensuring compliance with international standards.
Factory Audit
Common Questions About Factory Audit, Answered (FAQ)
A factory audit evaluates a manufacturing facility’s adherence to industry standards, regulatory requirements, and contractual obligations. It is designed to ensure consistent product quality, a safe working environment, and ethical practices.
A factory audit is crucial because it helps to maintain supply chain efficiency, reduce risk, ensure compliance with regulations, optimize costs, and foster strong business relationships between buyers and suppliers.
A factory audit checklist is a comprehensive list of items that must be evaluated during a factory audit. It includes quality control, manufacturing processes, equipment maintenance, material control, employee training, and environmental, health, and safety (EHS)
The frequency of factory audits depends on various factors, such as the size and complexity of the facility, the supplier’s track record, and the level of risk associated with the products or services being provided. However, it is generally recommended to conduct factory audits regularly to maintain supply chain efficiency and mitigate risk.
If a supplier fails a factory audit, corrective actions must be taken to address the issues identified. The supplier may be given some time to implement the corrective actions. A follow-up audit may be conducted to verify that the corrective actions have been taken. If the supplier fails to address the issues identified, the buyer may consider terminating the relationship.
BLOG
Related Articles
Trust our expert team of highly experienced inspectors to thoroughly inspect your products before
shipment, minimizing risks and ensuring compliance with international standards.
shipment, minimizing risks and ensuring compliance with international standards.