Quality control (QC) is a core component of success in the manufacturing and export-import business. In the past few years, consumer markets have been rocked by several large scale quality issues. From confectionery to pet food, motor vehicles, and even medical products, behind each case, there is evidence of disregard of quality control best practices leading to losses in the billions. But, the most disheartening consequence is the millions of consumers affected by the events. Most quality issues are avoidable. You need to exploit quality control services.
How can Tetra Inspection help you?
What is Quality Control? | Who is a Quality Control Inspector?
Quality Control Inspections Services
Quality control inspectors will visit your manufacturer’s factory to ensure the process and products meet the standards agreed upon before shipping to you. Quality control services include on-site factory inspections and testing with detailed reports to help ensure that your products meet your specifications and manage product quality in your supply chain. The most commonly used quality control inspections services are product inspections.
What is the Product Inspection?
Product inspections are used by quality control inspectors to assess whether the product conforms to AQL level, design requirements, and specifications. Quality control inspectors conduct product inspections at any stage of the production process to highlight the quality and regulatory issues early. This provides you ample time to take corrective measures if products do not conform to quality requirements. Product inspection is a part of on-site quality control inspections services.
On-site Quality Control Inspections Services
On-site quality inspection services require inspectors to visit the producer’s factory at any stage during manufacturing to monitor the process based on the requirement of the supplier or buyer. Inspectors focus on the client’s requirements. There are five types of on-site quality control inspections:
Inspection services are conducted as a quality control chain where the inspector undertakes one product inspection or quality check at a time. To avoid mix-up, your quality control inspector will a comprehensive quality control checklists.
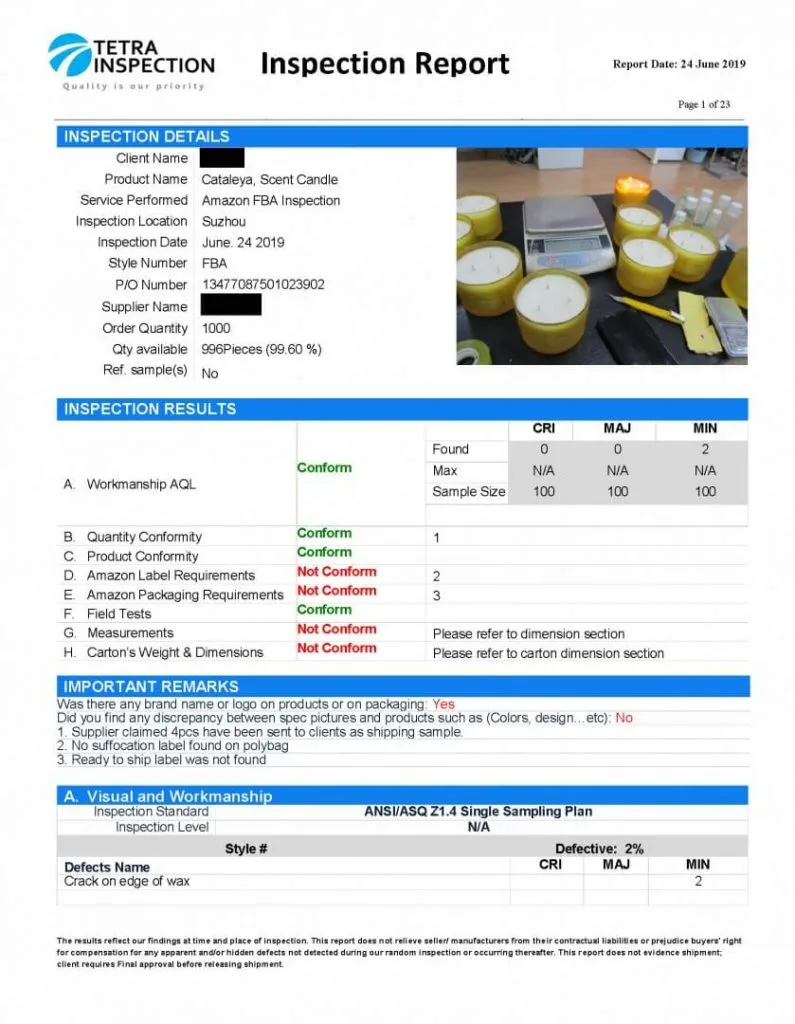
Initial production checks start before production begins and focus on clarifying the requirements and specifications to ensure the manufacturer can deliver the quality needed. Inspectors can also assess the manufacturer’s process, expertise, and materials. The checks can last until 20% of production has been completed to allow inspection of the first items to be manufactured. This step is known as First Article Inspection and can highlight defects to be corrected before the start of mass production.
Also known, On-Line Inspections, During Production Inspection (DUPRO), is an on-site quality inspection service conducted in the early stages of production when about 20% of the batch has been produced. It can highlight any defects early for correction.
Pre-Shipment Inspection (PSI) involves a systematic inspection of a sample selected randomly from all the batches already produced. It is conducted based on ISO standard sampling procedures to ensure the accuracy of the results. PSI is carried out near the end of production when at least 80% of the units in the whole order have been produced.
Container loading check focuses on ensuring that all the batches are packed correctly for shipping. Inspector checks the total quantity and for different sizes, colors, and styles in shipments. They also ensure the safety of the products during shipment using packing materials like Styrofoam.
Production monitoring is conducted on-site to inspect factory processes and implementation of specifications. PM can enhance accountability and professional working relationship.
Pre-Customs Clearance Inspection is carried out before the dispatch of shipments. It includes the visual checking of packages, quantity, commercial invoices, and so on.
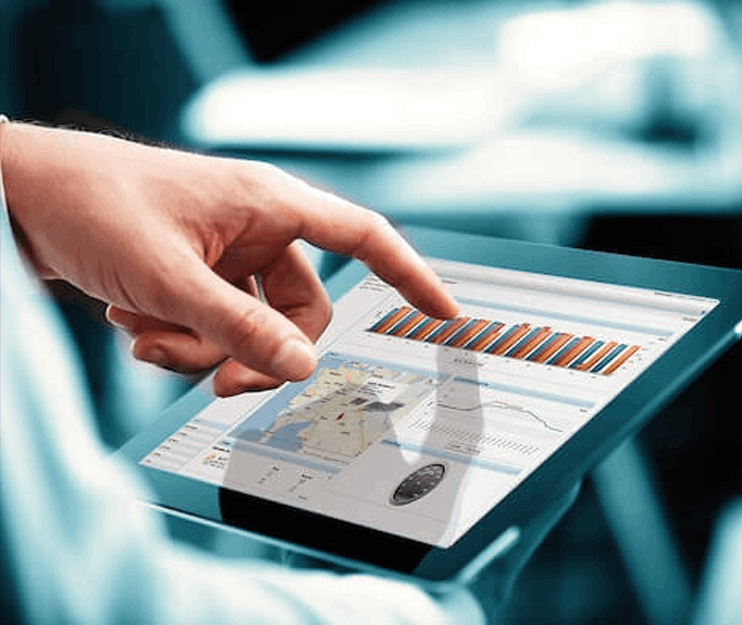
What is Quality Control?
Quality control is the measurement of the actual quality of a given program and diagnosing errors. Adhering to QC best practices is the most effective way to avoid quality issues. Quality control services include quality checks that are conducted either at the manufacturer’s factory, known as on-site inspections, or off-site checks done away from the factory. Inspections for soft lines and hardlines are conducted according to the internationally recognized ANSI/ASQC Z1.4 (ISO 2859-1) statistical sampling procedure. During product inspection, the frequency and severity of the defects discovered, and tolerances are analyzed based on standard AQL (acceptable quality limits) to award a pass or fail. The tolerance level is agreed upon by the producer or supplier and highlighted clearly in the quality control checklist used by QC inspectors during the process. Inspections like PSI, quality checks, and audits are all combined and undertaken methodologically in Quality Control Chain. To ensure the accuracy of QC results, you need to choose the right quality control inspector.
A quality control (QC) checklist, also known as the inspection checklist, is a criteria sheet to clarify product requirements. Five key elements should be outlined extensively and clearly in your quality control checklist:
Product requirements: To avoid confusion, product requirements should specify materials to be used, and specifications like weight and dimensions. You can include a sample with the color for comparison. For electronics, including labeling and markings like CE mark.
Packaging requirements: An effective quality control checklist clarifies how the products should be packaged, including weight, dimensions, and labeling requirements like size, contents, and markings. Labeling is particularly important if the cartons convey your brand.
On-site quality checks and tests: To avoid non-compliance and quality issues, you should list the tests and inspections, outline tolerances, and specify pass/fail criteria.
Defect classification: It is used to determine whether the product passes or fails the inspections. Defects under AQL standard are classified into three types – minor defects, major defects, and critical defects that should not be tolerated.
Constructive collaboration between all parties in a quality control chain is vital for success. You have to outline how all parties will collaborate during the inspection and start by consulting your supplier and QC staff as you develop your QC checklist.
The other types of quality control services include QC checks, QC audits, and quality assurance.
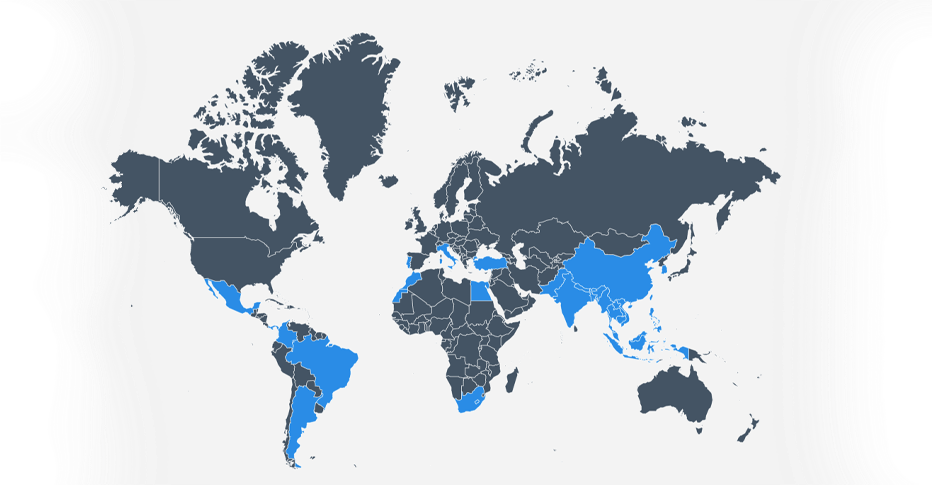
Quality Control Testings
On-site quality control lab tests
This type of quality check is usually conducted during product inspections. Most quality issues tested on-site are common or known issues and undertaken in the factory’s labs or test areas. On-site lab tests can highlight the raw materials used on your product. QC inspectors can test for hazardous chemicals to ensure your product does not violate regulations or pose safety risks.
Off-site quality control lab tests
Off-site quality checks involve highly advanced lab tests in controlled environments. A sample is collected and sent to a well-established lab for advanced testing like functionalities, usability, and safety. If the contract specifies the delivery of lead-free products, the inspector can take a sample to test for lead in a lab. Off-site lab tests are useful in quality control checks and ensure your products conform to safety regulations.
Quality Assurance Services
Quality control audits are conducted when importers and retailers are searching for the right partner to supply the products they need. It mainly focuses on evaluating if a potential supplier can deliver the client’s requirements. Most experienced quality control inspectors like Tetra Inspection offer Manufacturing Audits and Ethical Audits as part of quality control services, which include:
- Verification Audit: This is conducted to verify the authenticity of a potential supplier.
- Social Audit: QC inspectors use this audit to assess the ethicality of supplier’s social practices.
- Factory Audit: It assesses the capability and capacity of the potential supplier to deliver.
- Environmental Audit. Quality control inspectors evaluate if the supplier’s operations degrade or pollute the environment.
- Specific Audits. These are unique audits for specific importers, and sellers like Amazon FBA used to evaluate whether a company qualifies to supply products to Amazon sellers.
Quality control audits should be conducted by profession according to international standards. These audits can protect your brand against ethical and operational risks and also ensure safe working conditions in your supply chain. The profile of potential suppliers can help you choose the right supplier for your business.
services can help identify long-term solutions to resolve recurring safety and quality concerns in manufacturing companies.
Quality Assurance Services By Tetra Inspection
Quality assurance services help you deliver products that comply with global, federal, and state requirements. This QC service is highly effective for quality control in manufacturing and can address the root causes of quality issues in factories. Quality control inspectors administering quality assurance services integrate into the company to determine any operational shortcomings that hinder compliance. They also work with departmental heads and in-house teams to address issues in the client’s specifications. Quality assurance services can help identify long-term solutions to resolve recurring safety and quality concerns in manufacturing companies.