Heavy equipment forms the backbone of industries such as construction, mining, manufacturing, and logistics. The performance and safety of machinery like bulldozers, forklifts, cranes, and excavators are critical to operational efficiency and the well-being of workers.
Heavy equipment acts as the core foundation of industrial sectors such as manufacturing and construction. Security, reliability, and functionality are essential factors to consider when it comes to heavy equipment quality control.Â
Â
While procuring machinery from overseas, guaranteeing rigorous quality control becomes vital for brands or buyers to mitigate any logistical breakdowns and adhere to safety guidelines.
Â
This article will explore key concepts of heavy quality control, from the essential aspects of heavy equipment quality control, including processes, challenges, solutions, and best practices.
Â
Whether you are a manufacturer, supplier, or buyer, understanding the nuances of quality control can help you maintain high standards, reduce operational risks, and enhance the longevity of your equipment.
Without any further delay, let’s dive right in!
Â
What is Heavy Equipment Quality Control
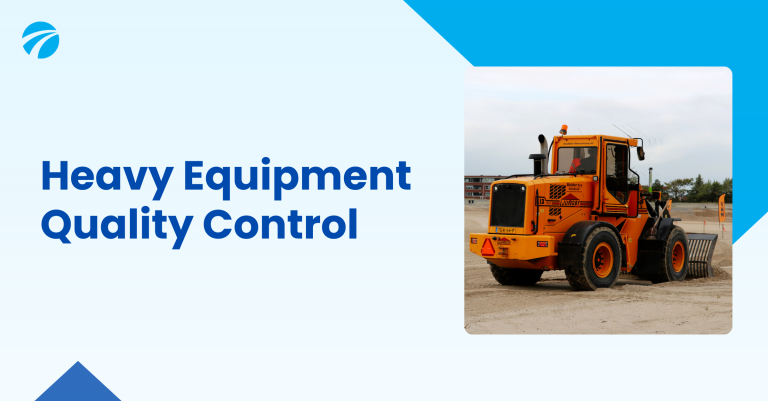
Heavy equipment quality control refers to the systematic processes implemented to ensure that machinery meets specified standards of performance, safety, and reliability. It involves a series of inspections, tests, and evaluations conducted at various stages of the production and supply chain. Quality control is not just about identifying defects; it’s about preventing them, enhancing product reliability, and ensuring compliance with international standards and regulations.
In the heavy equipment industry, quality control is essential to certify that bulldozers, forklifts, cranes, etc, operate properly and meet safety standards. With thorough heavy equipment inspection, the QC system helps identify technical issues in real time, mitigate site risks, and plan further for adjustments. All the steps involved in heavy equipment inspection ensure a seamless delivery of the final product to the clients. We will discuss more about the QC process in this article as we go forward.
What is the importance of Heavy Equipment Quality Control?
With growing complications in the heavy equipment industry, businesses are struggling to reach the premium quality standards that clients expect. An important factor to consider in the quality control for heavy equipment is the increasing pressure on manufacturers since the production of machinery components is now more complex than ever.Â
Â
Therefore, the importance of machinery quality control must be stressed more. Any negligence in the process of heavy equipment inspection can cause equipment failure, leading to decreased productivity and financial losses.
Â
However, with meticulous quality control measures, businesses can eliminate the risk of loss projects and establish themselves as trusted suppliers.
Heavy equipment quality control plays a key role in promoting effectiveness and boosting output by :
- Ensuring optimal performance by guaranteeing maximum efficiencyÂ
- Enhancing safety by boosting security measures
- Increasing equipment longevity by boosting machinery lifespan
- Lowering repair costs by minimizing defects ahead of time
- Reducing downtime by limiting potential operational lagsÂ
Key Elements Of Heavy Equipment Inspection
While heavy equipment quality control is now acknowledged on a bigger scale, it is crucial to understand the key factors of quality control implementation. We have tried our best to jot down the key elements of the QC process to ensure optimal results. Let’s take a look!
Â
Visual Inspection
Â
A QC expert inspector checks visually for signs of defects or machinery tear and wear. This method is one of the first steps for machinery quality control and helps to detect faulty components. Inspectors also look for signs such as cracks, corrosion, misalignments, and leaks.
Â
Material Testing
Â
Assessing the quality and properties of materials used in the equipment to ensure they meet required specifications. This may involve hardness testing, tensile strength testing, and chemical analysis.
Â
Functional Testing
Â
This approach checks for the equipment’s performance level and ensures that every part of the heavy equipment system works effectively. It evaluates the operational performance of equipment under normal and simulated conditions to ensure all components function correctly.
Â
Calibration and Performance AnalysisÂ
Â
Calibration is vital for heavy equipment inspection as it checks for accurate metrics, assuring machines function under the producer’s prescribed limits. Along with data analysis, reviewing fuel consumption rates and output levels is also vital to detect concealed issues in the equipment
Â
Load Testing
Â
For lifting equipment, load testing verifies if the equipment is capable of reliably carrying specific weights without any risk. This is a crucial element as exceeding loading capacity can bring about severe accidents on site.Â
Â
Dimension Check
Â
Understanding the dimensions of heavy equipment is vital for risk-free and productive operations. The key metrics for dimension include height, width, length, weight, volume capacitors, and other structural dimensions. These dimensions aid in deciding if designated parts fit properly and can accommodate the required load, helping prevent overloading the heavy equipment.
Â
Safety Testing
Â
Safety testing is an accumulation of multiple key elements of heavy equipment inspection. It involves operational checks to evaluate machine performance, routine inspections to detect defects, and load testing to check equipment capacity for handling loads safely. This element also includes checking the functionality of emergency measures such as alarms. Moreover, sufficient training is also vital here to ensure that workers adhere to strict protocols and instant emergency response. Safety testing primarily aims to reduce safety hazards and prevent operational disruptions.
Â
Vibration and Shock Testing
Â
Vibration and shock testing are essential as they involve external simulation of mechanical impact and shaking on different heavy equipment to conduct imitation tests. These tests aid in assessing how heavy equipment reacts to sudden shocks or
continuous vibrations – which helps determine the equipment’s structural capacity, reliability, longevity, and durability.Â
Â
Weld Quality Inspection
Â
The weld inspection method assesses that the welds of heavy equipment are safe, sturdy, and fit to operate. Critical aspects of weld inspection include checking the material’s evenness or uniformity, absence of any residue, smooth exteriors without permeable holes, and tightened weld joints. Additionally, visual inspections are frequently performed before, during, and after weld inspection to identify faulty base fusion, weak joints, or residue spatter.It is necessary to ensure that the right electrode and filler metals are used in building the welds for heavy equipment.
Â
Common Defects Found During Heavy Equipment Quality Control
Even though a reliable quality inspection team ensures that they detect every defect and make every adjustment necessary, it is very common to find subtle defects in heavy machineries. Let us take a brief look into the classic defects that inspectors must always watch out for.
Â
Welding DefectsÂ
Minor issues of cracks, porosity and weak weld base quality can compromise the structural integrity and strength of the equipment.
Â
Paint and Coating Issues
Â
Poor paint work and botched coatings can lead to eventual corrosion of the metal parts of the equipment, and even make paint layers to detach.
Â
Mechanical Defects
Â
Misaligned parts and improper assembly of bolts can lead the equipment to lose balance or create excessive vibrations.
Â
Engine Performance Issues
Â
A clogged exhaust system can come to take part due to internal engine defects and lead to overheating of the equipment.
Â
Wear and Tear
Â
Several components of the equipment, such as treads or belts have the tendency to wear out quite fast, and can end up preventing the machinery from meeting regulatory standards.
Â
The Process of Heavy Equipment Quality Control
Quality control for heavy equipment is a critical process that encompasses every stage of production, from the initial preparation to the final shipment. Implementing thorough inspections at each phase ensures that the machinery meets all safety, performance, and regulatory standards.Â
Â
Here is a concise overview of how quality control is performed at each stage:
Â
Initial Production Inspection (IPI) for Heavy Equipment
Initial Production Inspection is the first step in the quality control process. Here, inspectors assess raw materials, verify that they meet specified standards, and review the production setup. The purpose of IPI is to ensure that the supplier or factory understands the requirements for the final product. During this stage, inspectors also check for compliance with industry regulations and confirm that the equipment’s design specifications align with client expectations. Any early deviations are noted and corrected to avoid further complications as production progresses.
Â
During Production Inspection (DPI)Â for Heavy Equipment
Conducted when production is around 20% to 80% complete, the During Production Inspection allows for a mid-process assessment to catch potential defects early. Inspectors examine the workmanship, material quality, and assembly of components, ensuring that initial quality standards are maintained. By performing DPI, manufacturers can adjust production practices, fix issues, and verify that quality standards are consistently met throughout the production run. This stage is critical to prevent costly rework or delays by addressing issues before they are embedded in the final product.
Â
Pre-shipment Inspection (PSI)Â for Heavy Equipment
The Pre-Shipment Inspection takes place once the production is nearly complete, typically when the equipment is 80-100% finished. Inspectors conduct a final evaluation to ensure that each unit meets the client’s specifications and is free from defects. PSI involves a series of on-site tests to confirm the equipment’s readiness for real-world applications. This stage also includes packaging and labeling inspections to ensure safe transportation and compliance with international shipping standards.
Â
Field Tests in the Process of Heavy Equipment Quality Control
Heavy equipment quality control consists of more underlying yet key processes that are involved in the three primary stages mentioned before in this article. Let’s take a look at the mechanism of the associated field tests that make the inspection processes of Tetra top-tier.
Â
- Material Inspection: This step entails inspecting the unrefined raw materials to detect any faults present, such as rust, cracks, and discrepancies.
- Surface Finish Quality: Following the fabrication procedure such as cutting and melding, the product-specific texture of coating of the outer layer is checked for evenness to judge its uniformity which facilitates in finding defects, uneven spots, or rough finishes.
- Dimensional Accuracy: The precision concerning measurements of products is vital to guarantee that all parts of the equipment can be assembled accurately, for example, the length, width, and thickness of the parts are verified according to the project specifications to eliminate faulty challenges at the time of assembly.
- Welding Quality: Visual evaluations are carried out to detect external surface level defects, while Non-Destructive Testing (NDT) techniques including ultrasonic and radiographic examinations produce enhanced information about the welding effectiveness.
- Functional Tolerance:
Ultimately, operational capacity measures the equipment’s capabilities to resist any functional or performance-related pressure. Additionally, load, durability and pressure evaluations are also carried out to confirm that each component operates as needed during dynamic environmental conditions, and, instant adjustments are executed in case functional issues emerge.
Â
Types of Heavy Equipment We Inspect
At Tetra Inspection, ensuring the highest heavy equipment quality lies in our core values. We provide inspection services with the utmost commitment for a diverse range of heavy equipment machinery featuring but not limited to :
Â
- Forklifts
- Cranes
- Tractors
- Excavator
- Loaders
- Bulldozers
Essential Testing Standards for Heavy Equipment and Machinery Inspection
Heavy equipment quality control must always incorporate international standards and industry measures to ensure the security and optimal functionality of the machinery. At Tetra, we are working every day to make sure that our inspections are updated to adhere to the highest industry standards. Some of our key testing standards of inspection are:
Â
ISO 9001: This particular benchmark defines our parameters concerning the performance oversight system, and, is adopted broadly across most large-scale heavy equipment manufacturing inspections
Â
ANSI/ASME Standards: These America-specific standards include machinery design, safety regulations, and equipment testing performance.
Â
API (American Petroleum Institute) Standards: This standard is especially utilized for machines with usage in the gas and oil industry, they also conform to functionality and safety benchmarks.
Â
OEM Specifications: Each manufacturer and their factories possess particular regulations for equipment maintenance and inspection, which is essential to ensure optimal performance of heavy equipment machinery.
Â
Tetra Inspection’s Expertise in Heavy Equipment Quality Control
At Tetra Inspection, we are committed to providing top-tier heavy equipment inspection services. Our team of experts utilizes the latest quality control tools and adheres to international standards to ensure your equipment meets the highest quality benchmarks.Â
Â
Contact us today to learn how we can assist you in maintaining excellence in your heavy equipment operations.
Â